チョコ停とは?
ドカ停との違いや原因・対策について解説
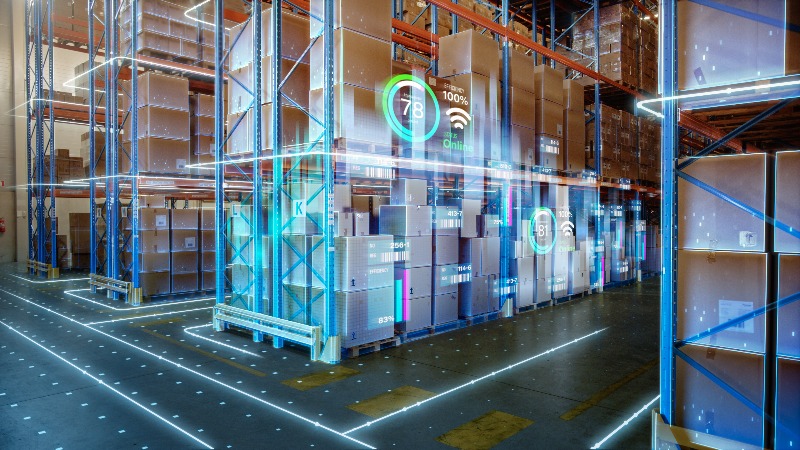
製造現場で起こる、ラインなどの生産設備が少しの間停止してしまうトラブルをチョコ停と呼びます。チョコ停は大きな問題ではないと思われがちですが、重なって発生してしまった場合、現場に様々な影響を与えるため対策が必要です。本記事では、チョコ停の概要やドカ停との違い、具体的なチョコ停対策などをご紹介します。

チョコ停とは
チョコ停と「チョコっと停止」の略称で、製造現場におけるライン設備がほんの少しの時間だけ停止してしまうトラブルのことです。
例えば以下のようなケースがチョコ停にあたります。
- 金属や木材を加工する際に発生する削りくずがそのまま残っているために、工作機械が正常に作動せず、業務が数分停止してしまう。
- 製造ラインで製品や部品がどれくらいの数の、どれくらいのスピードで流れてくるのか、適切に設計されておらずラインが詰まってしまい、業務が数分停止してしまう。
なお、チョコ停には、似た用語としてドカ停があります。続いてはチョコ停とドカ停の違いを解説します。
チョコ停とドカ停の違い
チョコ停とドカ停は、JIS規格においてそれぞれ詳しく説明されています。
チョコ停の説明は以下の通りです。
「設備の部分的な停止又は設備の作用対象の不具合による停止で,短時間に回復できる故障を小故障(通称としてチョコ停)という。」
引用元:JIS Z 8141:2001 生産管理用語 設備管理 番号6108
また、ドカ停は次のように記述されています。
「設備が生産ラインなどの大規模なシステムの一部となっていて、システム全体を停止に至らしめるような重大又は決定的な故障を大故障(通称としてドカ停)」
引用元:JIS Z 8141:2001 生産管理用語 設備管理 番号6108
ドカ停とチョコ停の違いは、トラブル発生後の復旧にかかる時間です。
なお、チョコ停は設備の異常や劣化の兆候であるため、放置しているといずれドカ停につながる恐れがあります。
チョコ停が現場に与える3つの影響
チョコ停は小さなトラブルではありますが、現場にはさまざまな悪影響が及びます。ここでは具体的な影響を3つご紹介します。
影響①:納期の遅延
チョコ停が重なると、製造工程全体の稼働率が低下してしまうため、納期の遅延につながる可能性があります。納期が遅れると、結果的に企業の信頼損失にもつながってしまいます。
影響②:品質の低下
製造の流れが止まってしまうことで、製品の品質低下や不良品の増加を招く恐れがあります。例えば、成形時にチョコ停が起きてしまった場合、成形不良となり廃棄の原因となります。また、チョコ停の復旧は人為的に行うため、ヒューマンエラーが発生したり、異物が混入したりと品質低下につながる可能性があります。
影響③:安全上のリスク
チョコ停からの復旧作業中は、製造における安全上のリスクがあるため注意しなければなりません。
例えば、溶接機のチョコ停を復旧するために、オペレータは設備を停止させてから対処を行いますが、チョコ停の原因である引っ掛かりを取り除いた途端、設備が残圧で動いてしまうことがあります。突然設備が動くことで、大けがの原因になる可能性があります。
このように、チョコ停によって生じる影響は決して小さくないため、チョコ停を発生させないための根本的な原因への対策が必要です。
チョコ停の原因
チョコ停が発生する代表的な原因として以下が挙げられます。
・定期メンテナンスの不足
設備のメンテナンスを怠っているとチョコ停を引き起こすことがあります。定期的なメンテナンス不足が原因で起こる設備停止のうち、修理を伴わずに復旧できるものはチョコ停に該当します。例えば、削りくずを掃除しなかったために起こる設備停止はチョコ停です。
また、金型のメンテナンス不足もこれに該当し、チョコ停を引き起こします。
以下記事ではチョコ停の金型のメンテナンス不足によるリスクをご紹介しています。あわせてぜひご覧ください。
・ラインバランスが不適切
ラインバランスの設計が不適切だとチョコ停を引き起こす可能性が高くなります。例えば、何を、どのくらいの数・速度で流すかを適切に設計できていない製造ラインでは、工程上で詰まりや引っ掛かりを起こしやすくなります。
・材料、仕掛品に品質のバラつきがある
前工程で加工された材料の品質にバラつきがあると、次工程でのチョコ停リスクが増加します。このような事態を回避するためには各工程の一元管理と、不良品の選別の対策が欠かせません。
・センサー類の読み取りエラー
センサー類は環境や経年劣化により、認識精度が低下するため、チョコ停を引き起こす原因となりえます。
チョコ停を減らすためには、実際にチョコ停がどれほど起きているのかを把握するということが重要です。続いては、チョコ停率とその算出方法を紹介します。
チョコ停率と算出方法
現場にてチョコ停がどれくらい起きているのかは、チョコ停率を算出することによって把握することが可能です。以下ではチョコ停率の算出方法をご紹介します。
チョコ停率とは
チョコ停率とは、生産設備の稼働時間のうち、チョコ停した時間の割合のことです。チョコ停対策を行う際に、チョコ停によってどのくらいのロスが生じたのかを数値で把握することに役立ちます。
チョコ停率の算出方法
チョコ停は以下の計算式で算出できます。
● チョコ停率 = (チョコ停時間/稼動時間)×100
なお、上記計算式の「稼働時間」は以下3つの時間の合計となります。
● 稼動時間 = 可動時間 + チョコ停時間 + 空転等の時間
例えば1日の中で、可動時間が23時間、チョコ停時間と空転等の時間がそれぞれ30分であれば、
(0.5時間/24時間)×100となり、チョコ停率は2%(小数点以下は切り捨て)であることがわかります。
チョコ停対策の3ステップ
ここでは、チョコ停対策を行う際の手順をご紹介します。ポイントは、まず数値を把握したうえで、原因を明確にし、具体的な対策を実行することです。
ステップ①:チョコ停によるロスを数値化する
まず、チョコ停によるロスの数値化を行います。
手法としては、ワークサンプリングという調査があり、トラブル発生の要因や従業員・機械の動作状況、かかった時間や工数などを調べます。チョコ停対策においては、工場設備を稼働と非稼働に分け、さらに非稼働は設備トラブル・チョコ停・段取り替えに分類することが重要です。
ワークサンプリングによる調査でチョコ停の時間が明確化されたら、稼働率を以下計算式で算出できます。
● 稼働率(%) = 稼働時間 / 負荷時間
※ 負荷時間…1日もしくは1カ月のうち設備が稼動しうる時間
● チョコ停を入れた稼働率(%) = 稼働時間 / (負荷時間 + チョコ停時間)
上記2つの稼働率の差分が、チョコ停による稼働率低下を示します。
ステップ②:データの分析と原因の特定
チョコ停によるロスを数値化できたら、分析と原因の特定を行います。
まずは、ワークサンプリングによって判明したチョコ停の原因と発生回数を記録します。記録するデータが少ないと詳細な分析ができないため、発生の都度記録しておきましょう。
そして、データが集まったら、パレート図を活用して、チョコ停が発生した時に優先して改善すべき原因を特定します。パレート図とは、ある項目の度数を大きい順に並べた棒グラフと、その累積比率を表す折れ線グラフを組み合わせた図です。
チョコ停対策において、縦軸は「発生の件数と割合」、横軸は「発生要因」として、分析を行うことができます。
ステップ③:対策の実施
パレート分析で原因を特定した後は、優先度の高い原因の対策を検討します。この時、対策を実行するかはチョコ停の損失額を見て決めることがおすすめです。損失額は以下計算式で算出可能です。
● チョコ停1回の損失額 = チョコ停の時間 × 時間あたりの生産個数 × 製品の単価
また、対策の実施に合わせて「予知保全」を行うこともポイントです。予知保全とは、設備の不具合の兆候を検知し、故障を事前に防ぐことであり、重大な事故や、設備の老朽化を防ぐことが可能です。
なお、予知保全の他にも「予防保全」があります。予防保全とは、あらかじめ決めておいた機械が使えなくなるとされる期間や使用できる回数に従って部品の交換を行う保全方法です。突発的なトラブルによる稼働停止時間を減らしたり、機械設備の保全管理をしたりするのに役立ちます。
以下では予防保全の目的やメリット、事例を詳細に解説しています。あわせてぜひご覧ください。
IoTを活用したデータ収集でチョコ停を削減
今回紹介した手順でチョコ停対策をするには、まず正確なデータの収集を行う必要があります。
そこで、データを正確かつ効率的に収集するにはIoTの活用が有効です。IoTとは、あらゆるものをインターネットでつなぐ技術のことであり、製造業にIoTを導入することで、人手では煩雑になりがちな管理を自動的に行えるようになります。
IoTの活用によって、設備の部分的な停止といったチョコ停の正確なデータの収集が可能です。また、データによってチョコ停をみえる化することで、具体的な対策を講じ、生産性を向上することができます。
このような製造におけるIoT活用の事例を以下資料でご紹介しています。ご興味のある方はぜひ一度ご覧ください。
お役立ち資料はこちら
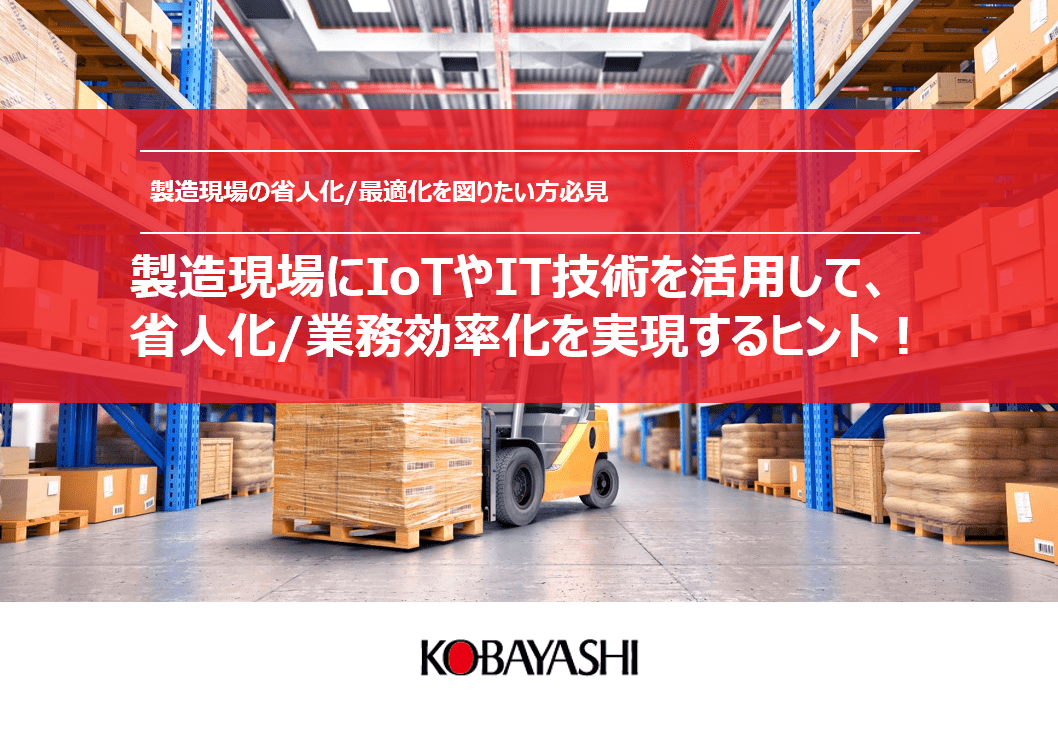
お役立ち資料
省人化/業務効率化を実現するヒント!

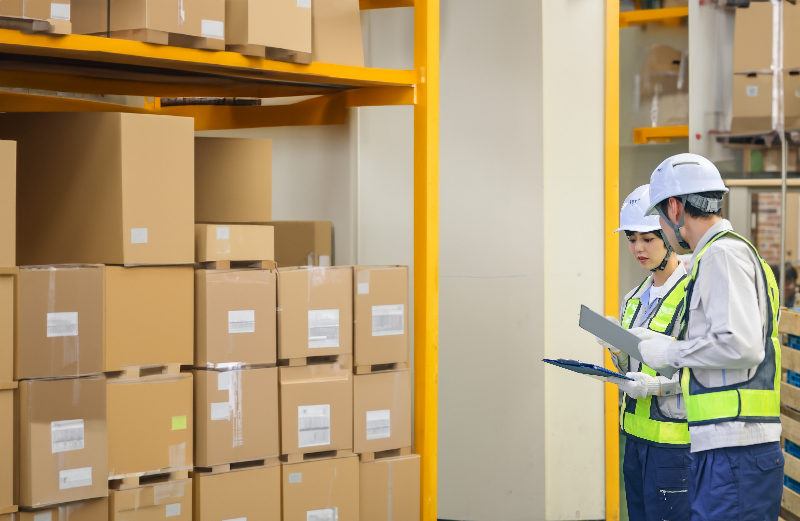
対策とは?
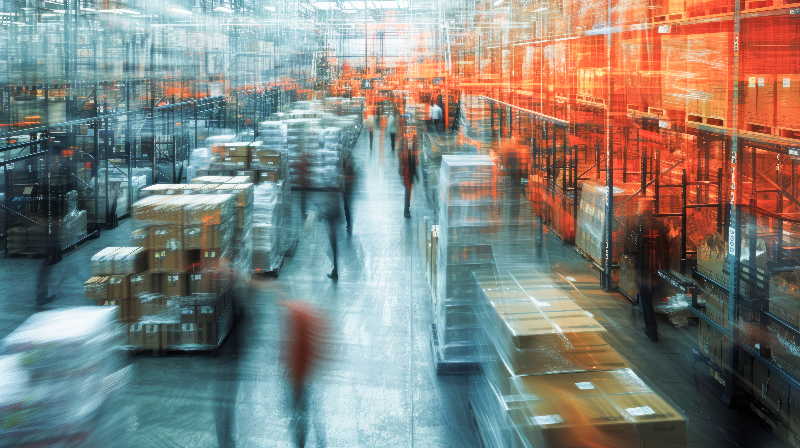
発生する原因と影響、対策を解説
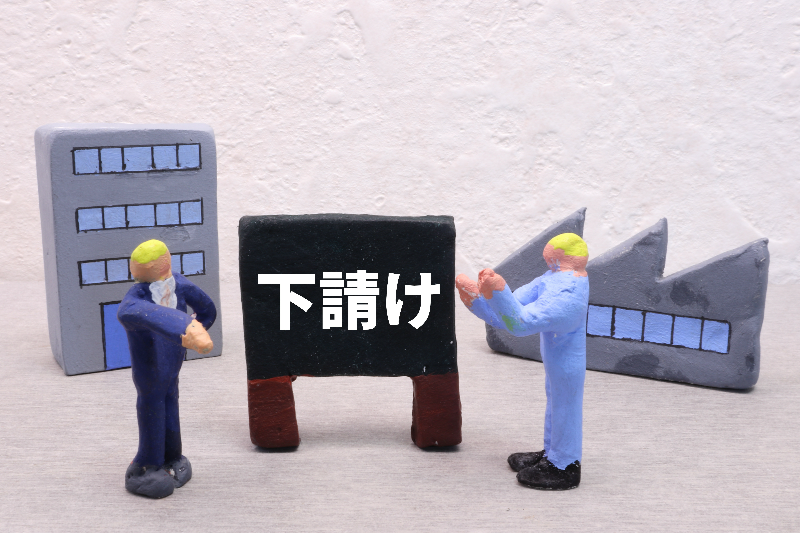
適切に行うポイントとは?