ボトルネック工程はどこにある?
見つけ方と改善に向けたステップ
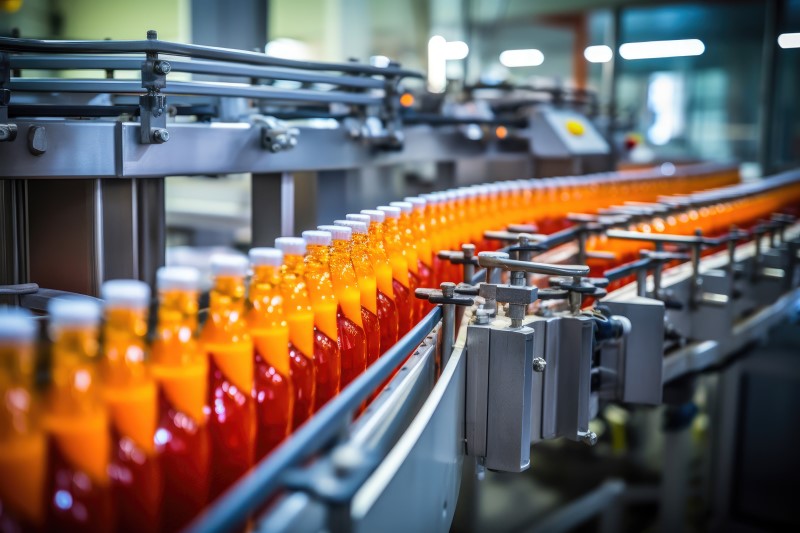
製造現場のボトルネック工程は、工程全体の生産性に大きな影響を及ぼすものであるため、どこにあるのか探し出して解消することが不可欠です。そこで本記事では、ボトルネック工程の見つけ方や解消のためのステップなどを解説します。

ボトルネック工程とは
ボトルネックが生産工程に存在することの影響
ボトルネック工程とは、製造業での生産管理において、生産能力・生産効率が最も低くなっている工程のことです。ボトルネック(bottle neck)とは、もともとは飲み物などの瓶の一番細くなっている「首」の部分を指す言葉であり、その部分で液体の流れが滞ることに由来します。
ボトルネック工程が生産工程に1か所でも存在すると、他の工程の生産性をどれだけ高めても全体として生産性を高めることができません。つまり、最も生産性の低い箇所が全体の生産性に大きな影響を与えます。
例えば、以下のような生産能力の工程①~③があるとします。
・工程①:20個/時間
・工程②:20個/時間
・工程③:5個/時間
上記の場合、工程①・②で処理された製品(1時間あたり20個ずつ)が工程③に流れます。しかし工程③では1時間に5個ずつしか製品を処理できないため、全体の生産能力は5個/時間となります。
このように、ボトルネック工程が全体の生産性向上を妨げてしまうため、解消が不可欠です。
なお、製品の製造過程を工程ごとに管理し、調整・運営することは「工程管理」と呼ばれます。工程管理の詳細については、以下の記事をご覧ください。
ボトルネック工程の見つけ方
ボトルネック工程は以下の点に注意すると見つけやすくなります。
・生産が停滞している工程
生産が停滞している箇所を探すことが最も確実な見つけ方です。生産が停滞していると前工程で仕掛品や部品が滞留していたり、作業員が待機していたりすることが多く、ボトルネック工程となっている可能性が高いと考えられます。
・稼働率が高い工程
一見、稼働率が高いことは良いことのように思えますが、あまりに稼働率が高い工程があると、他の工程に追いつくためフル回転の状態になっている場合があります。そのため、稼働率の高さもボトルネック工程を発見する際の1つの要素となります。
・製品1単位あたりの作業時間が長い工程
1単位あたりの作業時間が長いということは、生産効率が低いということです。そのため、特に作業時間が長い工程はボトルネック工程になっている可能性があります。
・不良品やトラブルが生じやすい工程
不良品やトラブルが発生しやすいと生産ラインが停滞してしまいます。トラブルが多いとその工程に無理が生じている可能性もあり、さらなるトラブルを招くことでボトルネック工程になる傾向があります。
【TOC理論】ボトルネック工程の解消ステップ
ボトルネック工程の解消方法として代表的なものに、TOC(Theory of Constraints、制約理論)と呼ばれる手法があります。以下では、TOCをもとにボトルネック工程の解消ステップを解説します。
ステップ①:ボトルネック工程を特定する
まずは、前章でご紹介したポイントをもとにどの工程がボトルネック工程になっているかを特定します。
その際には、各工程での作業時間を棒グラフで表わした「ピッチダイアグラム」の活用が役立ちます。ピッチダイアグラムの棒グラフが長い個所は作業時間が長くなっていることを意味しており、ボトルネック工程となっている可能性が高いです。
ステップ②:ボトルネック工程の作業能力を最大化する
次に、ボトルネック工程となっている工程に焦点を当て、作業能力を最大化できないか検討します。例えば作業フローを1つひとつ洗い出して、無駄な作業が生じていないかなどを確認し、それを解消することが重要です。
人員を増やすなどの手段で解消することも可能ですが、人件費が増えるためトータルでの費用対効果が高まらない可能性もあります。そのため、まずは既存の設備や人員をフル稼働させて生産性を高められないかを検討する必要があります。
ステップ③:他の工程の生産性をボトルネック工程に合わせる
他工程の作業スピードを落とすなどして、ボトルネック工程の生産力に他の工程を合わせることも方法の1つです。そうすることで仕掛品の余剰が発生しにくくなり、全体の生産がスムーズになります。また、他工程の人員をボトルネック工程に投入するなどの調整もしやすくなります。
ステップ④:ボトルネック工程の機能を強化する
以上のステップを踏んでも期待するような生産性向上が難しければ、新たな設備の導入・投資や作業者の増員・スキルアップなど、ボトルネック工程そのものの能力アップを図る必要があります。人員の配置見直しや、研修を通じたスキル向上といった人材面のアプローチに加え、機械化や新たなソリューション導入などにより、抜本的な効率化や生産性向上を進めることも重要な手段の1つです。
次章では、このようなボトルネック工程の解消に役立つソリューションをご紹介します。
ボトルネック工程の解消に役立つソリューション
音声認識入力システム
今でも「入力業務」や「情報の確認」といった工程を手入力やハンディターミナルで行っている現場も多く、こうした運用方法がボトルネック工程の発生の要因となっていることがよくあります。
手作業や目視確認などで対応している工程に音声認識入力システムを導入することで、生産性の向上が可能です。例えば部品・製品の精度測定と結果の入力に関して、キーボード入力を音声入力に変更することで、精度測定をすると同時に音声で数値を入力する仕組みを構築し、業務時間を大きく短縮した事例があります。
また、仕分け工程において、ハンディターミナルの画面に表示された指示内容に基づき仕分けを行っていたため、手が塞がり、目線も製品や仕分け先から外れるという課題に対し、作業者がヘッドセットを装着し音声で指示を得ることで、作業効率がアップしミスの削減につながった事例もあります。
弊社がご提供している音声認識入力システムについては以下の資料をご覧ください。
RFIDソリューション
無線通信によって情報をやり取りできるRFタグ・ラベルを専用のリーダーで読み取るRFIDを導入することで、在庫管理や物流工程の最適化を進めることができます。
例えば、製品にRFタグ・ラベルを取り付けることで、検品時に製品を1つずつ読み取らずにRFIDリーダーにより一括で読み取ることが可能です。これにより作業の時間や負担を軽減でき、ヒューマンエラーの発生も防げるためボトルネック工程の解消に役立ちます。
RFIDを活用した製造現場の改善アイデアについては、以下の資料をご覧ください。
以下の資料ではボトルネック工程の解消に関連して、製造現場でIoTやIT技術を活用することで省人化/業務効率化を実現するヒントを詳しく解説していますので、ご興味のある方はぜひご覧ください。
お役立ち資料はこちら
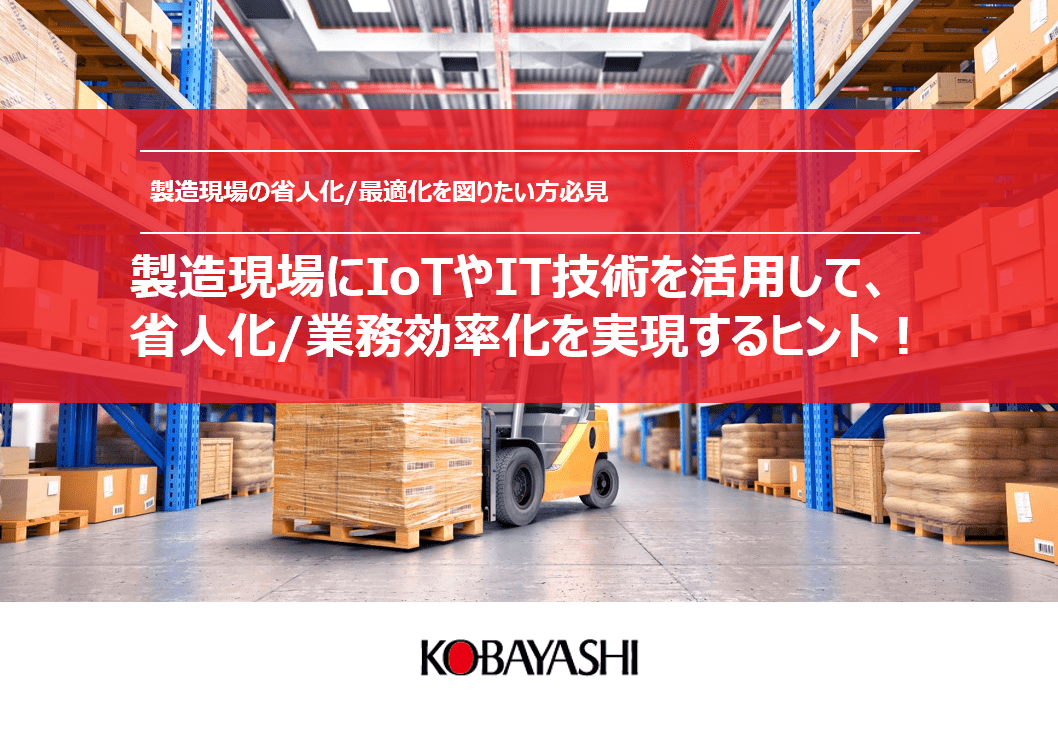
お役立ち資料
省人化/業務効率化を実現するヒント!

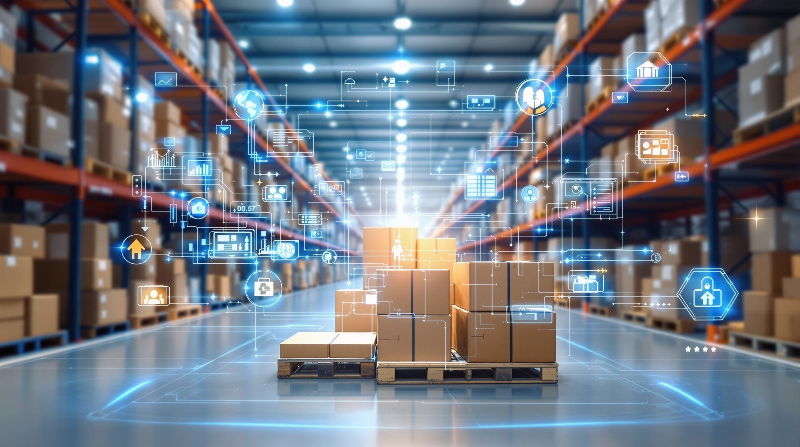
業務内容や効率化する方法を解説
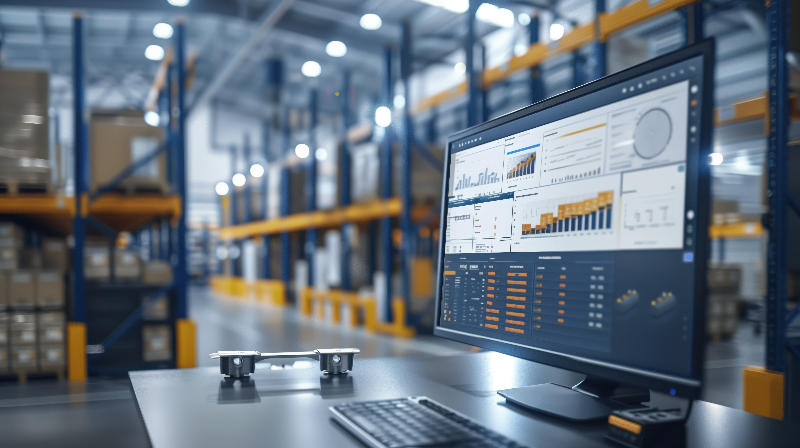
課題と解決策を解説
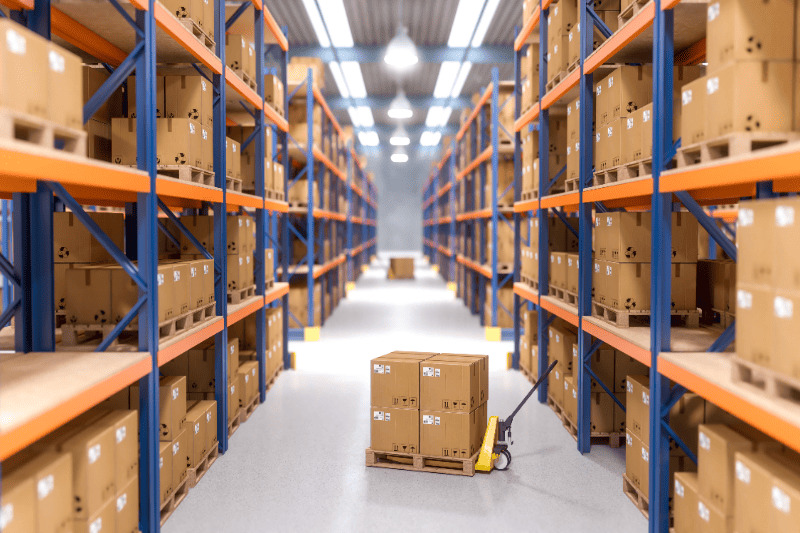
よくある課題、効率化する方法を解説