【製造業向け】部品ピッキングのミスを防ぐ
対策とは?
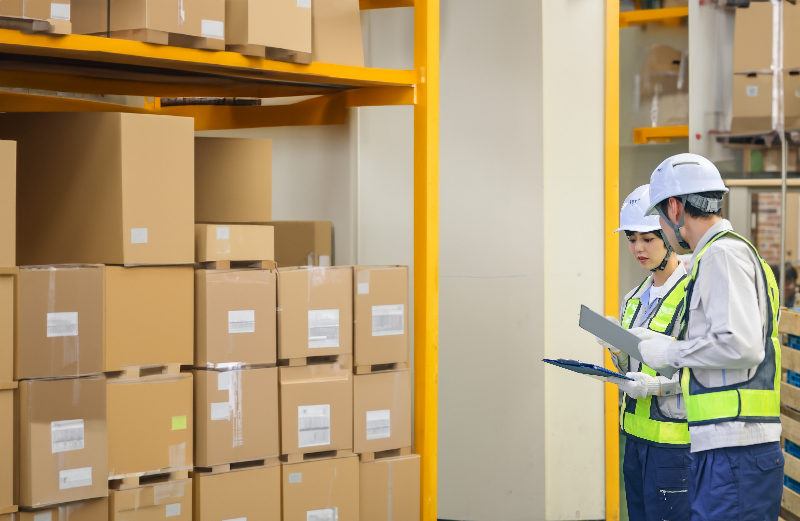
製造業において、部品ピッキングは製品を効率的に製造するために重要な工程です。しかし、目視確認に頼っていたり、ロケーション管理が適切に行えていなかったりするとミスが発生しやすくなります。このような課題を解決する方法の一つとして、バーコードや二次元コードによる管理方法を導入することが効果的です。
本記事では、部品ピッキングの方式やミスが発生する原因、ミスを防止するための方法を解説します。

部品ピッキングとは
部品ピッキングとは、指示書や伝票に従って必要な部品をピックアップし、集める工程のことです。
製造業においては主に、保管庫に置かれている部品の中から、製品の組み立て工程に必要な種類を必要な分だけ作業場所へと供給することを指します。
仕入れの段階では、部品は個々の製品や工程に合わせて分類されているわけではないため、受け入れた大量の部品を一度に作業場に置いておくと現場が混乱してしまいます。そのため、保管庫に一旦受け入れ、そこから必要な分をピッキングして現場に供給することが作業効率を高めるうえで重要となります。
部品ピッキングの方式
部品ピッキングの方式には以下の2つがあります。
摘み取り方式(シングルピッキング)
作業者がオーダーごとに必要な部品を倉庫内から直接ピックアップする方法です。「シングルピッキング」ともいいます。
ピッキングリストの記載内容に沿って順番にピックアップし、台車やカートに部品を載せていきます。該当する部品を集めた後は、仕分けをせずに組み立てラインに渡すことができます。
取り間違いが少なく、多品種少量生産の現場に適していますが、オーダーごとに倉庫を移動するため移動距離は長くなります。
種まき方式(トータルピッキング)
その日必要な複数の部品を一括でピックアップし、その後オーダーごとに仕分けていく方法です。仕分けエリアで部品を振り分ける「種まき」作業を行うことからこう呼ばれ、「トータルピッキング」ともいいます。
一度にまとめて部品をピックアップできるため、倉庫内の移動が最小限になります。また一括ピッキングと仕分けの分業により、大量のオーダーにも対応しやすいので大量生産の現場に適しています。
一方で、一括でピックアップした部品類を仕分けるための場所を確保する必要があるほか、検品や梱包を始めるまでに時間が要することが一般的です。
部品ピッキングでミスが発生する原因
部品ピッキングでは、目視確認やロケーション管理が適切に行われていないことに起因するミスがよく見られます。
目視確認によるヒューマンエラー
目視で出荷指示書と現物の確認を行っている場合、ミスが発生しやすくなります。
例えば、外観や品番が似ている部品が隣接して保管されている場合、作業者が誤って類似品を選んでしまうことがあります。必要な部品の数量を誤って認識し、過不足が生じることもあります。
特に、作業時間に余裕がない、人手が少ない、長時間勤務が常態化しているなど、作業者の精神的・肉体的負担が大きい現場ではヒューマンエラーが発生しやすいです。
また作業手順が標準化されておらず、人によってピッキングのやり方が異なる場合も、経験の浅い作業者を中心にミスにつながることがよくあります。
ロケーション管理が適切にできていない
適切なロケーション管理ができておらず、倉庫内のどこにどの部品が保管されているのかが把握できていないと、類似した部品や隣り合う部品を間違ってピッキングするミスが発生しやすくなります。
また、保管場所を固定しないフリーロケーション方式を採用している場合、部品の保管場所が常に変動するため、保管のたびに適切にロケーションを記録していないと部品の所在がわからなくなり、正しい部品をスムーズにピッキングできなくなります。
一方で所在を把握しやすいように固定ロケーション方式を採用している場合、特定の部品の在庫が少なくても他の部品を置けないため、保管スペースの無駄が生じることがあります。
部品ピッキングのミスを防止するには
ピッキングに関する問題を解決するためには、バーコードや二次元コードを活用することが効果的です。
具体的には、ハンディターミナルやスマートフォンなどを使用して、部品に貼付されたバーコードや二次元コードの情報を読み取る方法です。
出荷指示情報と部品の照合が容易になり、目視に比べピッキングのミスを低減できます。
出荷時のバーコード活用について詳しくは、以下の記事をご覧ください。
部品ピッキングのミスを防ぐ対策を実践しよう
部品ピッキングは目視で行っているとヒューマンエラーを防ぐことは難しいため、バーコード・二次元コードの技術を活用することがおすすめです。
小林クリエイトでは、持ち歩きが可能なハンディターミナルを活用して、QRコードやバーコードの読取ができる誤品チェック/実績収集システム「ハブリッジシステム」もご用意しております。ピッキング作業の際、ハンディターミナルで「バーコード」や「二次元コード」を読み取ることで、正しい部品なのか照合が可能なため、ヒューマンエラーを削減できます。
ハブリッジシステムの詳細は、下記資料でご覧ください。
お役立ち資料はこちら
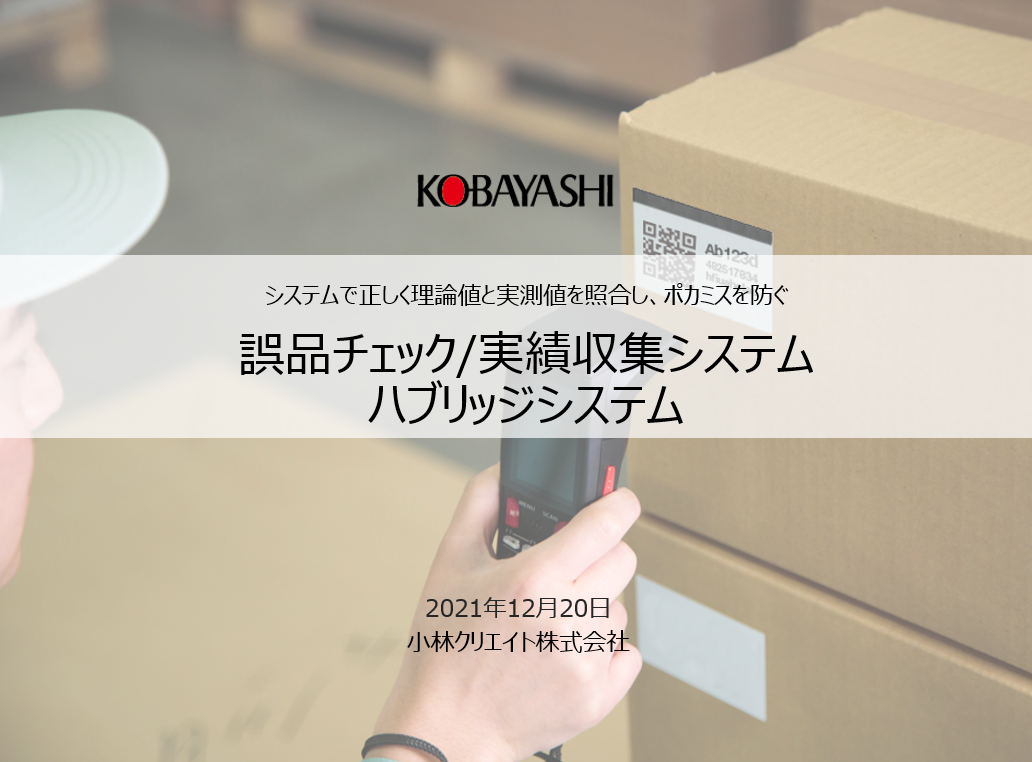
お役立ち資料
システム
「ハブリッジシステム」

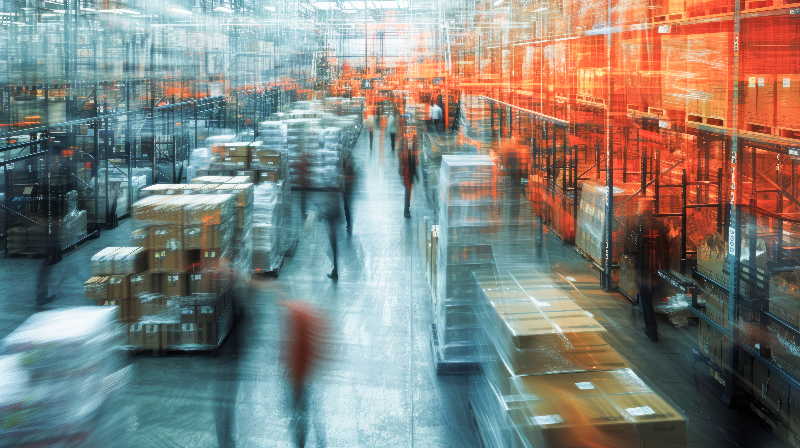
発生する原因と影響、対策を解説
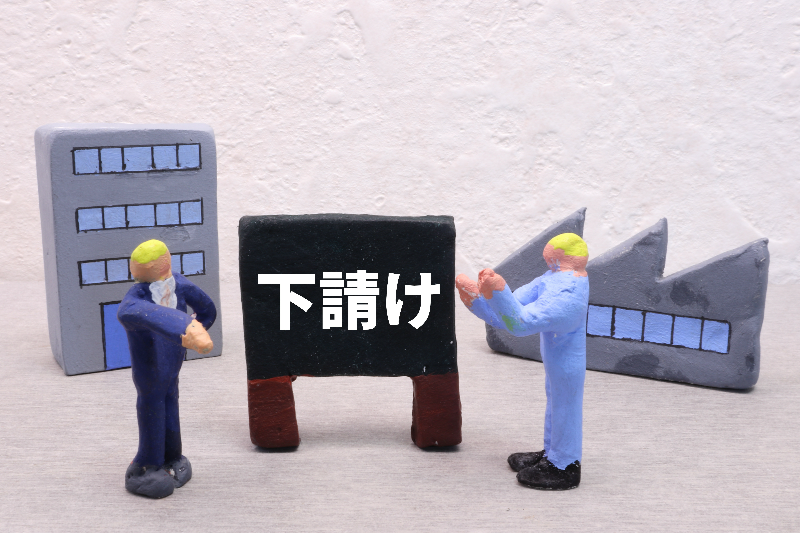
適切に行うポイントとは?
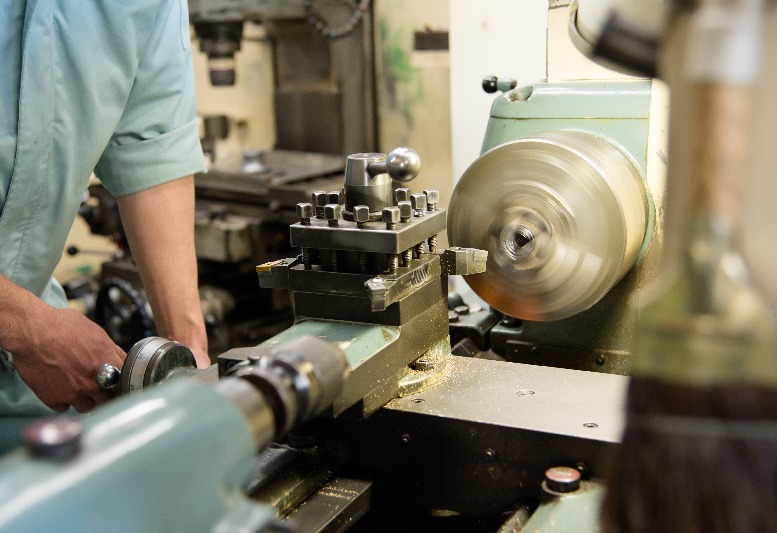
業務効率化の方法と事例を紹介