誤品を減らす生産管理のポイントは
バーコードにあり!?
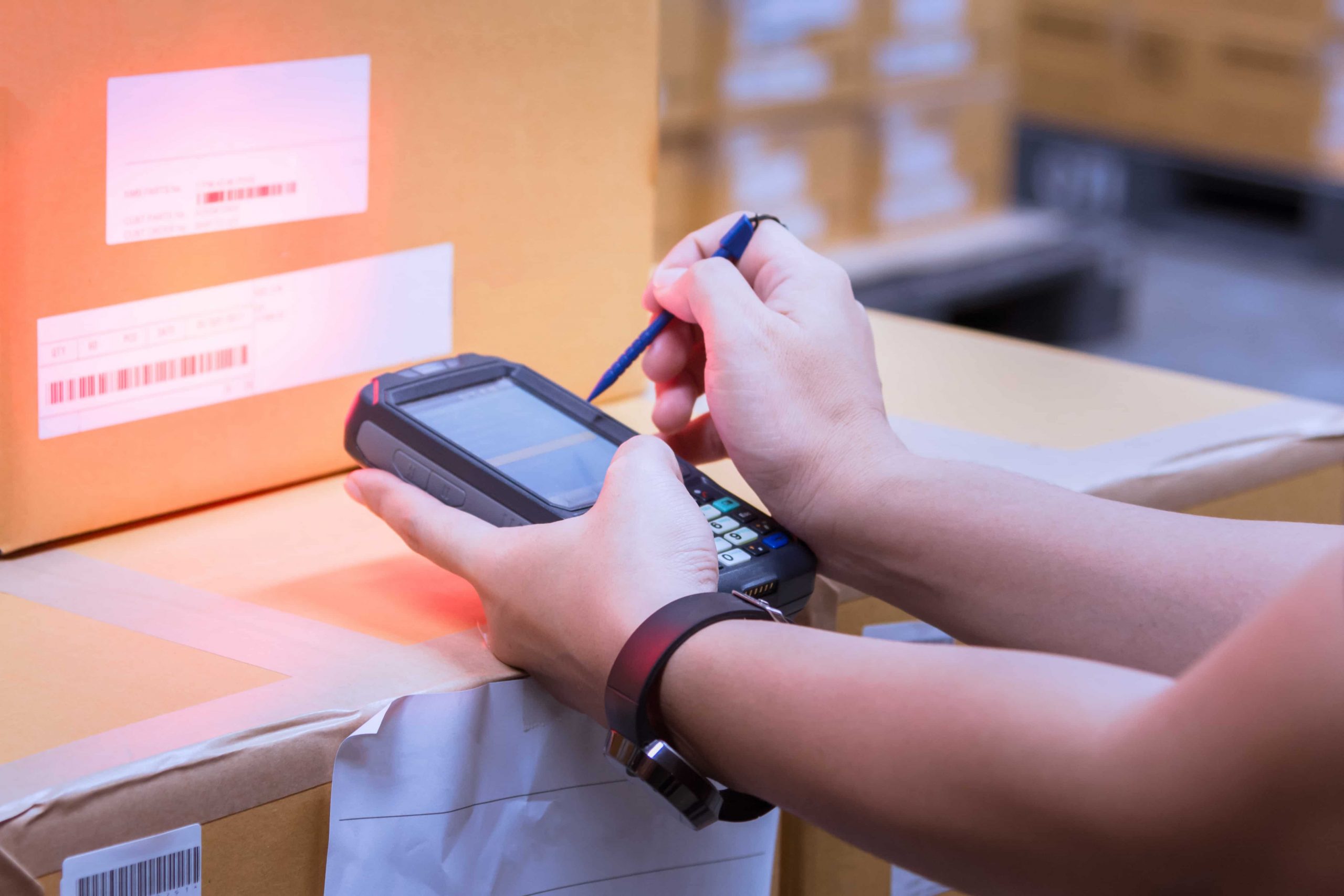
近年、部品調達のグローバル化により、荷物や供給ルートが多様化し、物流現場が複雑化しています。入出荷業務はいまだ人手に頼っている工場も多く、ヒューマンエラーによる誤品が後を絶ちません。このようなミスを防止し、品質向上に努めるためには企業としてどのような対応をとるべきなのでしょうか。
本記事では、誤品を減らす方法について紹介します。

誤品が起こる原因とは
誤品が発生する主な原因としては、以下の2つが挙げられます。
複雑化する入出荷業務
誤品が発生する背景には、近年のグローバル化による調達ルートの多様化があります。グローバル調達にはコストや競争力に大きな魅力がありますが、それに伴い調達ルートが多様化し、部品の欠品や不良があった際の対応も複雑になります。
また国内の取引においても多様な取引先から原材料が納入されており、各社によって出荷管理方法などが異なることも入出荷業務の複雑化に拍車をかけています。このような入出荷業務の複雑化が、誤品のリスクを高めている原因の1つです。
人の手によるチェック作業
また、入出荷業務はいまだ人手に頼っている部分も多いため、ヒューマンエラーによるミスが頻発してしまうことも誤品の原因として挙げられます。
出荷業務におけるヒューマンエラーを削減し、効率化を実現する方法については、以下の記事で紹介しております。あわせてご覧ください。
また、入出荷時における検品作業の省人化を図る方法については以下で紹介しております。ご興味のある方はぜひご覧ください。
製造業におけるよくある
チェックミスによる誤納品
誤品が発生すると、自社のみならず、取引先や消費者にまで影響が及び、企業の信頼低下やイメージ低下を招いてしまう恐れがあります。
製造業によくある誤品には現品票の見間違いや思い込みがあり、これらのミスはヒューマンエラーにより発生します。ヒューマンエラーを減らす対策としてよく行われるのがダブルチェックやトリプルチェックといった、さらに人による確認を増やすことでミスの軽減を図ろうという対策です。再発防止のためダブルチェックやトリプルチェックを導入するのもひとつの対策ではありますが、人によるチェックは確実性が薄く、ミスにミスが重なることで対策を潜り抜けた誤出荷が出てしまう場合があります。
製造業全般におけるヒューマンエラーについては以下の記事で詳しく解説しております。あわせてご覧ください。
このようなミスの対策としてバーコードリーダーによる読取を導入する企業も少なくありませんが、単にバーコードリーダーを導入しただけでは、読取漏れなどの新たなミスが発生する可能性があり、対策をしてもミスが減らないといったことになってしまいがちです。このような場合、そもそもなぜチェックミスが起きるのかを洗い出し、入出荷工程を一元管理しなければミスを減らすことはできません。
開発コストを抑えつつ
一元管理してミスを減らす方法
複雑化した入出荷業務に対応していくうえでは、多種多様な納入先を想定した標準化が必要不可欠です。
そこで各工程を標準化し、ミスを減らすために、入出荷工程の一元管理が重要となります。
一方で、工程の一元管理には作業毎に異なる予定データと実績データの照合条件に合わせた実績収集システムの開発や、取引先毎に異なる照合条件に合わせた誤品チェックシステムの開発が必要となり、多大なコストがかかってしまいます。
開発コストを抑制しながら入出荷工程の管理を実現するポイントは以下の記事で紹介しております。あわせてご覧ください。
次章では、1つのシステムで様々なバーコード読取や照合パターンに対応することで、開発コストを抑えつつ一元管理を実現できる小林クリエイトのソリューションをご紹介します。
開発コストを抑えつつ一元管理を実現
『誤品照合システム ハブリッジ』
そこで開発コストを抑えながらも、1つのシステムで様々な納入品に対応する方法として、小林クリエイトの「誤品照合システム ハブリッジ」をご提案します。
こちらのシステムでは、持ち歩きのできるハンディーターミナルを活用して、QRコードやバーコードの読取ができます。具体的な活用例として、現品票に記載されているQR情報を集荷リストとして登録したうえで集荷処理を行うことで、確実な集荷&出庫履歴の取得ができるようになります。
他にも、社内現品票と客先現品票の2点照合による、工程内のかんばん挿し間違い防止にも活用できます。
顧客ごとの現品票はそのままに、様々な現品票に付与されるバーコードやQRコードを設定することで、業務の標準化を実現します。
このような小林クリエイトのハンディーターミナルを活用した「誤品照合システム ハブリッジ」を導入することで、製品出荷時の現品票差し替えチェック、製品入出庫置き場のチェックなど、都度出荷データと照合し作業が進められるようになります。
取引先ごとにバーコード読取、照合パターンを自社でマスタ登録し運用できますので、取引先が増えても自社で誤品チェックの照合条件を追加設定が可能であり、開発コストを抑えることができます。
製品の詳細については以下の資料よりご覧ください。
今回は、誤品を減らす方法についてご紹介しました。弊社、小林クリエイトでは製造物流系産業で培ったノウハウを活かし、お客様の業務改善を幅広くサポートしております。
「IoT化の第一歩として何か取り組みたい」
「みえる化を促進して作業効率を上げたい」
とお考えのご担当者様は、是非資料をご覧いただき貴社の業務改善にお役立てください。
お役立ち資料はこちら
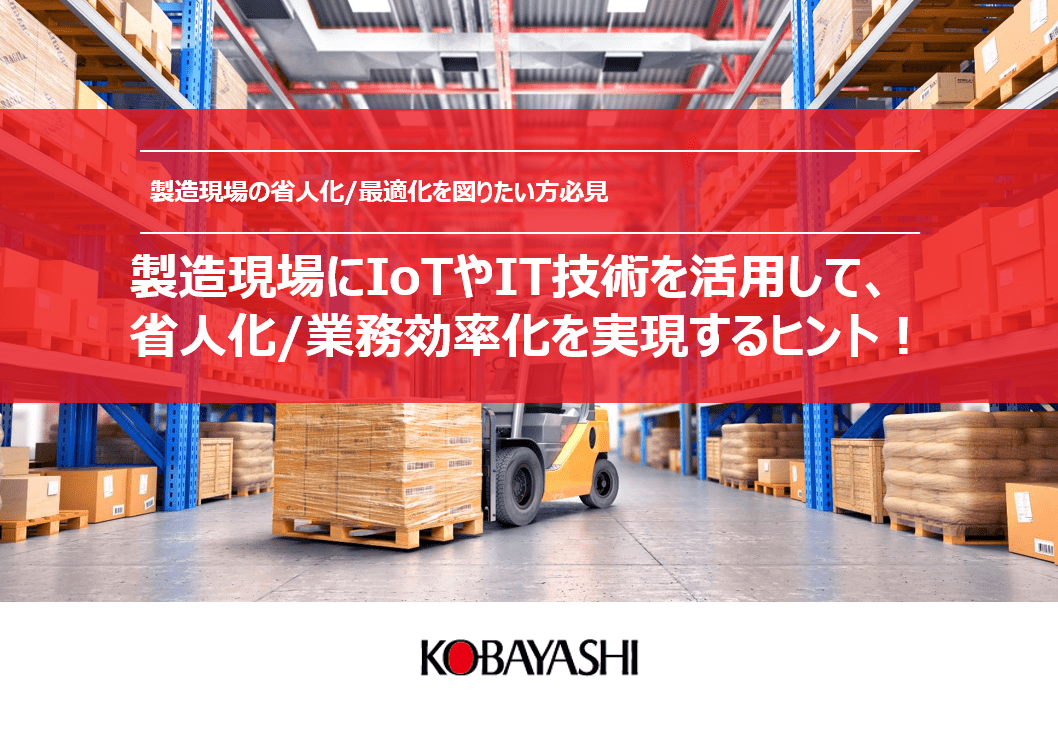
お役立ち資料
省人化/業務効率化を実現するヒント!

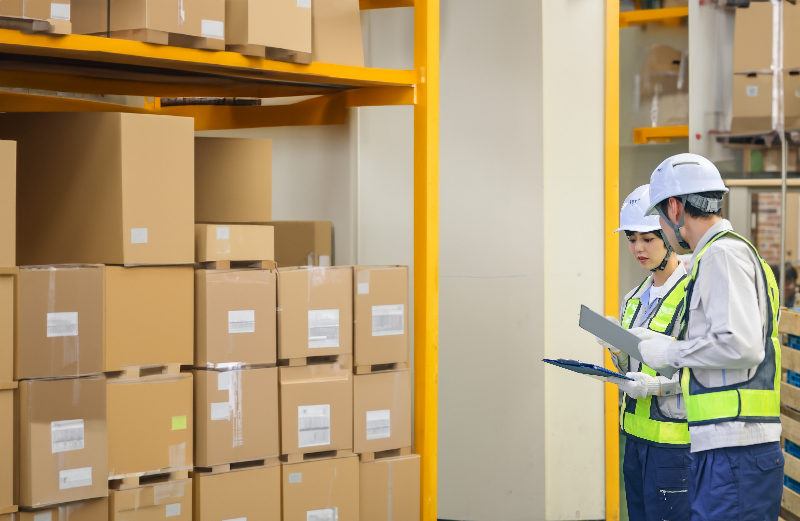
対策とは?
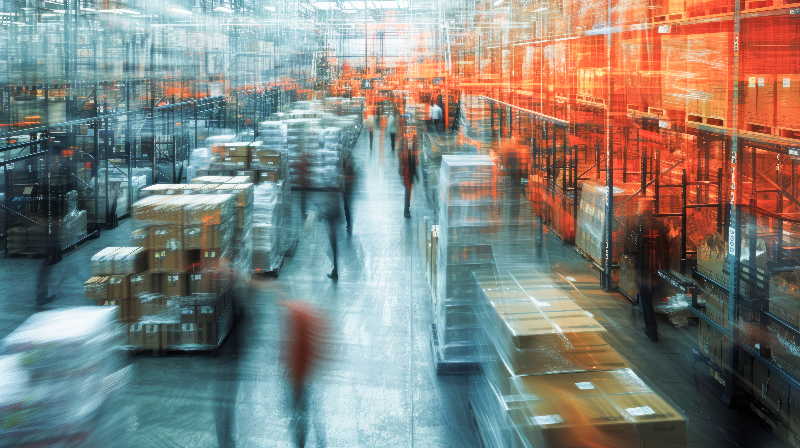
発生する原因と影響、対策を解説
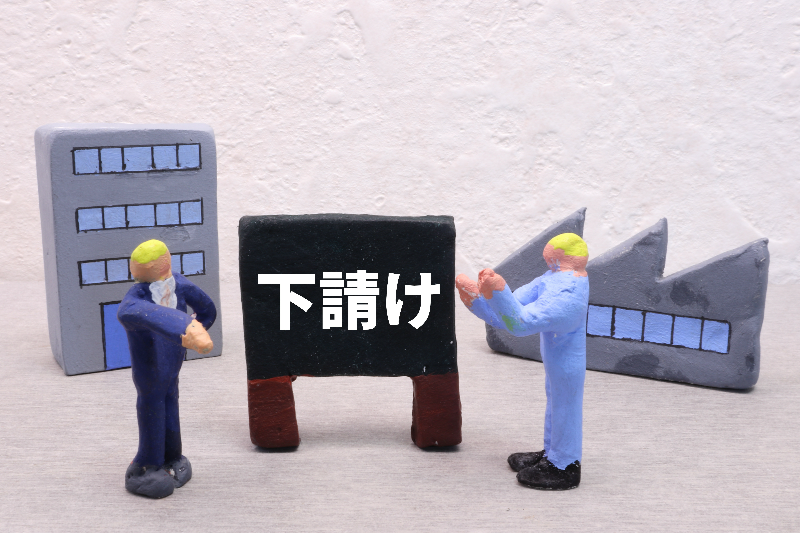
適切に行うポイントとは?