製造業の在庫管理を解説 -管理方法や
システムによる業務改善アイデアを紹介-
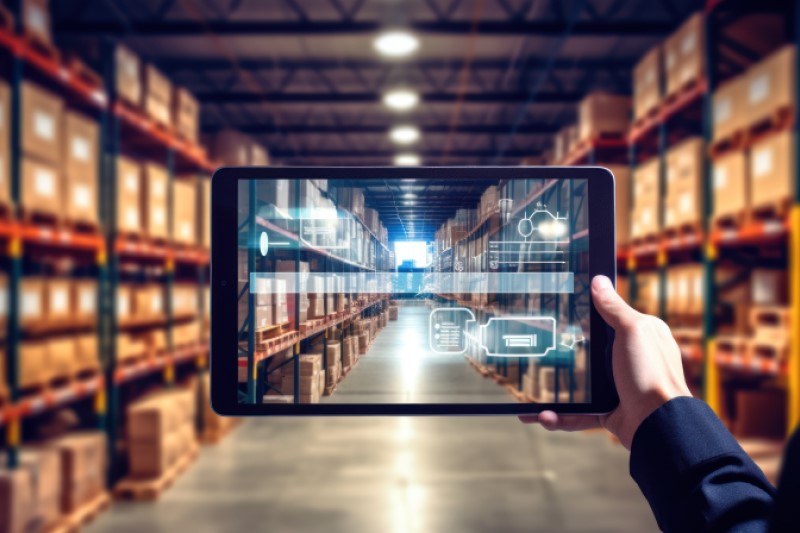
製造業において在庫管理は非常に重要です。在庫管理が正しくなされていない場合、余剰在庫の発生や販売機会の損失などが起きてしまう可能性があります。この記事では、在庫管理の目的や方法、ポイント、課題について分かりやすく説明しています。さらに、Excelや手作業によって生じる、在庫管理の問題点の解決方法も紹介します。在庫管理に関する知識や情報を得たい方はぜひ参考にしてください。

製造業における在庫管理
在庫管理とは
在庫管理とは、製品を適切な状態で供給しつつ、必要以上の余剰な在庫品が出ないように管理をすることです。
ここでいう「在庫」とは、完成した製品をはじめとした部品や原材料、仕掛品など現金化の可能性がある物全般のことを指します。また、在庫数を適量に維持することも「在庫管理」にとって重要です。
在庫管理の目的
在庫管理の主な目的は、在庫の量を過不足なく適切に維持することであり、以下のような効果が得られます。
- 過剰在庫による保管料の増加、倉庫スペースの圧迫、廃棄のための費用などのリスク防止
- 業務効率化、生産性向上
- キャッシュフローの健全化
上記のような効果を得るためには、適切な在庫管理の方法を把握しなければなりません。次章では、主な在庫管理の方法について解説します。
在庫管理の方法
在庫管理の主な方法は、ロケーション管理 ・ ABC分析 ・ 入出庫管理 ・ 棚卸の4つが挙げられます。
ロケーション管理
ロケーション管理とは、在庫や保管場所に番号やIDを振り分けることで、在庫が倉庫内のどこにあるかを把握・管理する方法です。在庫の場所を管理することで正確かつ効率的なピッキングが可能になります。
ロケーション管理の方法は、在庫の位置を固定する「固定ロケーション」、在庫の位置を自由に決める「フリーロケーション」、固定ロケーションとフリーロケーションを組み合わせた「ダブルトランザクション」の3つです。
固定ロケーションは、あらかじめ在庫の保管場所を固定し、そこから出荷する管理方法です。1つの製品に対して特定の場所を割り当てるため、在庫切れが一目で分かります。
フリーロケーションは、倉庫の在庫状況に応じて保管場所を変更する管理方法です。倉庫内の棚に空きが発生した際に、その都度そこに新たな在庫を保管します。そのため、保管スペースの無駄が無くなるというメリットがあります。
ダブルトランザクションは、固定ロケーションとフリーロケーションの両方を組み合わせ、倉庫内をストックエリアとピッキングエリアの2つのゾーンに分けて管理を行う方法です。保管効率と作業効率の両方を同時に向上させることができます。
倉庫業務において起こりやすい問題やその解決方法については、以下の記事で解説しているため、併せてご覧ください。
ABC分析
ABC分析とは、在庫状況をデータ化し、優先して管理すべき在庫はどれかを分析する方法です。管理の重要度が高い順にA、B、Cと優先順位を付けることから「ABC分析」と呼ばれています。
製品によって、エンドユーザーの需要やそれに基づいた製品の生産量は異なります。そのため、全ての製品の管理方法を統一してしまうと、ムダな作業やコストが発生する可能性が高まります。
そこで、ABC分析で在庫管理の優先順位を定めることで、人員や予算などのリソースを適切かつ効率的に配分できるようになります。
入出庫管理
入出庫管理とは、倉庫に入庫する在庫と出荷する在庫を記録することです。
適切な在庫管理を行うには、いつ、何を、どれだけ入出庫したかを正確に記録しておく必要があります。入出庫の日付、製品名、数量などの管理を徹底することで、在庫状況の把握や在庫過不足を抑制でき、在庫の異常がある場合にすぐに対応できるようになります。
また、効率の良い入出庫管理を実現するためには「入庫した在庫のうち、日付が新しいものから出庫する」という先入れ・先出しのルールを意識することが重要です。
以下の記事では、先入れ・先出しについて詳しく解説しています。入出庫管理の基本やRFIDを用いた業務改善にご関心のある方は、ぜひご覧ください。
棚卸
棚卸とは、帳簿上の在庫数と現場の実在庫数を照合する作業のことです。在庫の数量だけでなく、状態も同時に確認・評価します。通常は期首や期末に行い、正確な売上原価の把握や利益の計算、帳簿上の在庫数と実数の差分把握などのために行います。
従来は、作業員が1つひとつ数を数えて在庫確認を行っていましたが、昨今では在庫管理用のバーコードやICタグなどで在庫を割り振り、人的ミスの削減を可能にしています。
以下の記事では、棚卸業務を効率化する方法について詳しく解説しています。こちらも併せてご確認ください。
ここでは在庫管理の主な方法について説明しましたが、次章では在庫管理をするうえで重要なポイントについて紹介していきます。
在庫管理のポイント
在庫管理の方法を把握しても、確認すべきポイントを理解していなければ適切な在庫管理はできません。以下では、適切な在庫管理を行うために確認すべきポイント3つを紹介します。
現状の在庫を正しく把握する
適切な在庫管理の第1歩は、現場の在庫数を正しく把握することです。在庫を正しく把握していなければ、データ上の在庫と実物の数量が一致しなかったり、在庫の紛失や欠品に気付かなかったりするなど、業務効率が低下する恐れがあります。
在庫数を正しく把握するための取組はさまざまな企業が実施していますが、在庫数の確認を手作業で行っている場合、ヒューマンエラーの発生が問題となっています。
例えば、紙ベースの伝票管理、伝票と台帳の目視確認、入出庫データの手書き記入、Excelへ手入力などを行っていると、どうしてもミスが発生しやすくなります。
記入漏れや確認漏れなどにより、実在庫と帳票上の在庫数が一致しないことが頻繁に発生すると、情報の修正作業などに時間がとられ、他の業務へのリソースが削られてしまう恐れがあるため、効果的な対策が必要です。
在庫管理において、管理データと実数が一致している状態のことを「情物一致」といいます。ヒューマンエラーを防止し、情物一致を実現する方法については、以下の記事で解説しています。ぜひご覧ください。
適正な在庫数を定める
現状把握をした後は、どれくらいの期間でどれくらいの在庫数を確保すれば在庫管理が最適化できるかを想定します。適正な在庫数を定めるためには、在庫が一回転する期間を把握し、仕入れの数や頻度を計算することが重要です。
しかし、適正な在庫数を定めても、実際に在庫を保管している拠点の在庫情報がリアルタイムに共有されていなければ、在庫管理は煩雑なものになってしまいます。
例えば、調達時に拠点ごとの最新の在庫状況を正しく把握できなければ、ムダな発注や在庫不足が生じかねません。扱う在庫の数量が膨大になるほど、このような問題は大きくなり、在庫管理の業務に時間がかかりやすくなるため、対策が必要です。
在庫数を適正に近づける
現状の在庫の状態と適正在庫数を把握した後は、そのギャップを埋められるように計画を立て、在庫数を調整することが必要です。計画実行後は実際の結果を確認し、より適正在庫に近づけるためにはどのような改善が必要なのか分析をします。
しかし、実際の在庫管理業務は煩雑になりやすく、適正化のハードルが高いこともあります。特にイレギュラーな需要の増減に対して適正在庫の確保に苦戦し、在庫の不足や過剰を招くことがあるため注意が必要です。
次章では、こうした在庫管理の課題を解決し、業務改善・効率化を実現する方法を紹介します。
在庫管理システムによる業務改善アイデア
昨今では、さまざまな在庫管理システムを活用することで、業務改善が可能になっています。
Excelや手作業による在庫管理の問題点
Excelや手作業で在庫管理を行うと、作業工数が増えることで担当者の業務負担が増加し、入力ミスといったヒューマンエラーも発生しやすくなります。また、品数増加に伴う業務の複雑化や、属人化といった問題も発生やすくなります。
こうした人の手に頼った在庫管理の課題を解決する方法としては、在庫管理システムの導入が有効です。在庫管理システムによって在庫管理業務を標準化することで、手作業による入力ミスやチェック漏れを防ぐことができ、属人化の解消にも繋がります。
自動認識技術を活用した
システムによる在庫の「みえる化」
前述した問題点を解決する主な方法として、「二次元コード」や「RFID」などの自動認識技術を活用した在庫管理システムが挙げられます。
情報が埋め込まれたラベルやタグを対象物に取り付けて専用の機械で読み取ることにより、在庫管理におけるヒューマンエラーの削減や作業効率の向上が実現できます。また、読み取りした情報をシステムで一元管理することにより、在庫の「みえる化」を実現し、在庫の過不足解消にも繋がります。
二次元コードやRFIDによる在庫管理については、以下の記事で詳しく解説しています。
また、以下では、二次元コードを用いた棚卸システムの導入で、棚卸業務の効率化やヒューマンエラー防止を実現した企業様へのインタビュー記事がご確認いただけます。ご関心のある方は、こちらもあわせてご覧ください。
在庫管理の効率化は小林クリエイトにご相談を
小林クリエイトでは、二次元コードやRFIDをはじめとする、自動認識技術を活用した在庫管理効率化ソリューションを提供しています。RFタグを付与することで「何が」「いつ」「どこに出荷され」「どのくらいあるのか」を正確に把握・管理できるなど、在庫管理の適正化の実現が可能です。
弊社では、RFIDで在庫管理を行える「在庫管理システム」をご提供しています。
本システムを使用することで、入出庫情報のみえる化と棚卸作業の簡略化を実現できます。
在庫管理システムについて詳しくは以下の資料をご覧ください。
また、RFタグに関してあらゆる種類を取り揃えており、それぞれの現場での利用シーンごとに最適な提案が可能であるため、継続的な運用サポートを行えます。
以下の資料では、RFIDを用いた在庫管理や製造現場の改善アイデアを紹介しているため、興味のある方はぜひご覧ください。
お役立ち資料はこちら
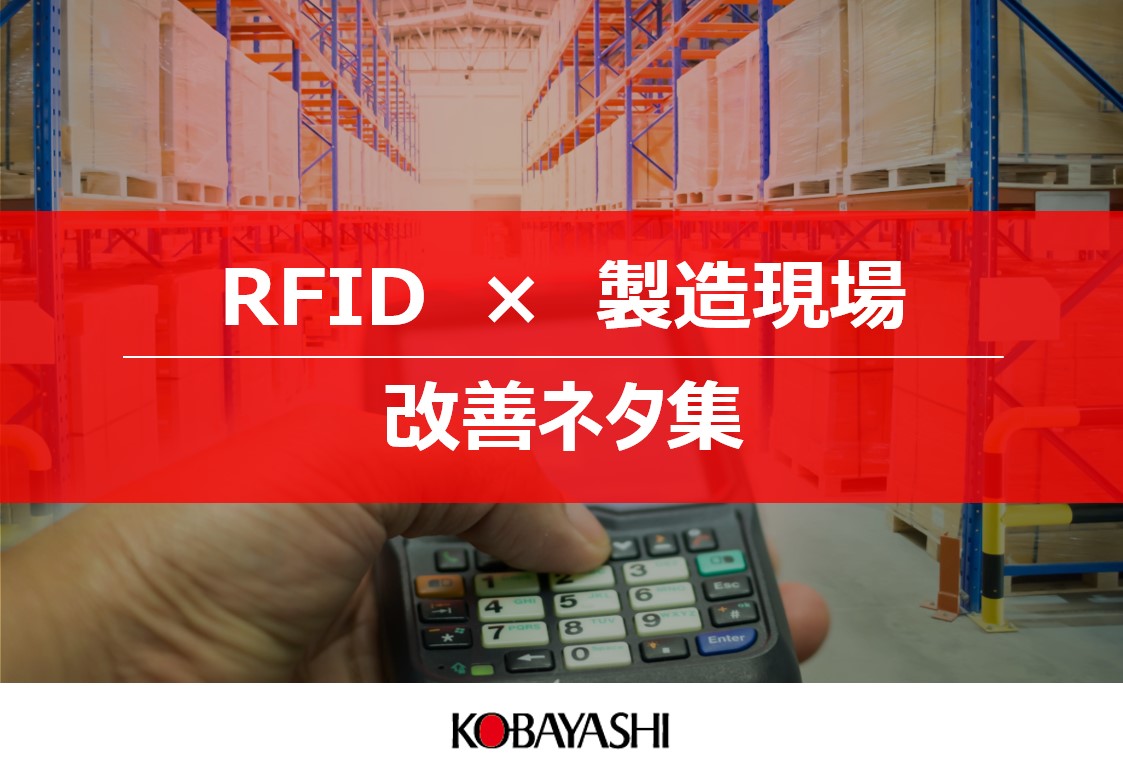
お役立ち資料
改善ネタ集

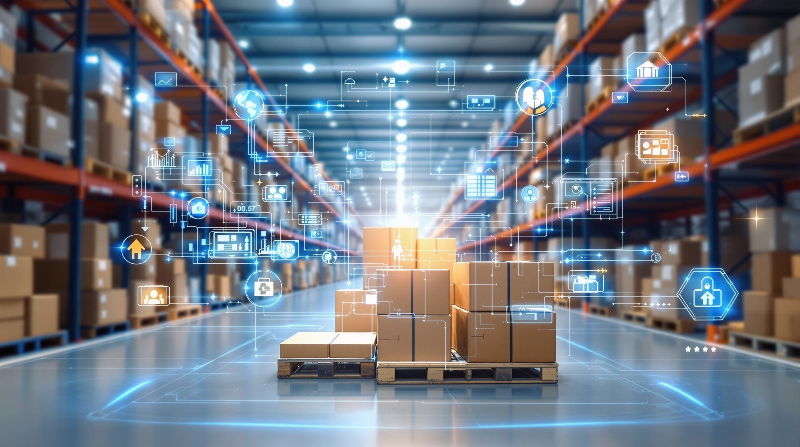
業務内容や効率化する方法を解説
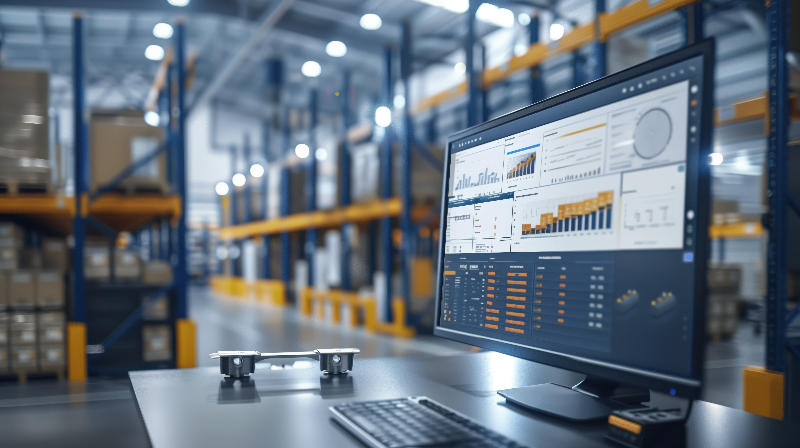
課題と解決策を解説
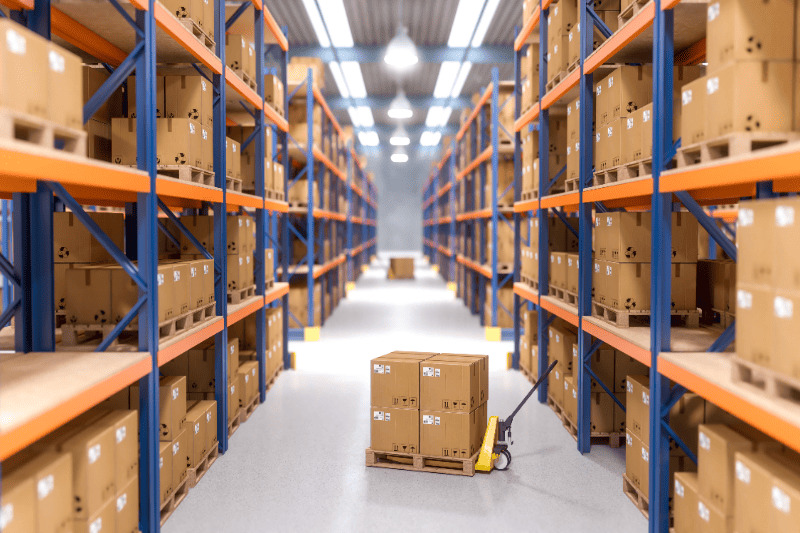
よくある課題、効率化する方法を解説