誤納品・誤出荷を防ぐには?
発生する原因と影響、対策を解説
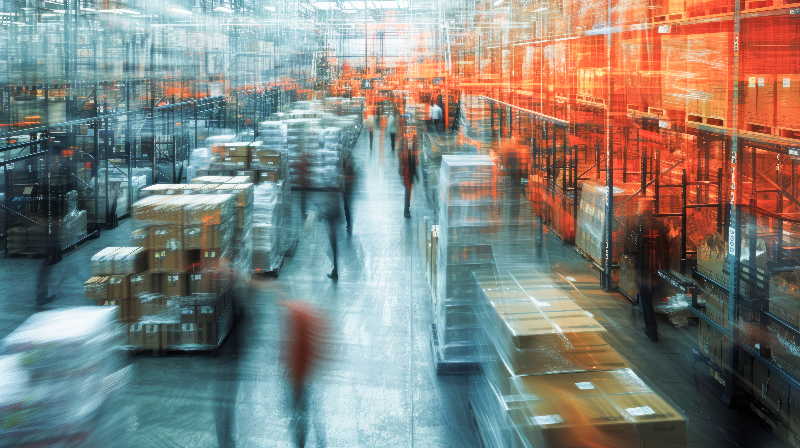
誤納品・誤出荷とは、製品や部品の数量、種類、配送先などを間違えてしまうことです。無駄なコストの発生や信頼低下を招くため、可能な限りゼロにしなければなりません。そのためには、ミスが発生する原因を知り、適切な対策を講じる必要があります。
本記事では、製造業において誤納品・誤出荷が起こる原因とその影響、防止するための対策を解説します。

誤納品・誤出荷が起こる原因
誤納品・誤出荷が起こる主な原因としては、以下の3つがあります。
出荷指示のミス
出荷指示のミスは、納品・出荷の初期段階で発生します。
よくある原因としては、受注システムにおける誤入力や、手書き指示書の記載ミス、指示をExcelに転記する際の記入ミス、などが挙げられます。品番、数量、納期、配送先情報などの記載間違いが典型例です。
指示自体は正しかったとしても、現場担当者への伝達が不十分なケースや、追加の出荷指示を口頭で受けたものの、記載を忘れたまま現場の従業員に渡してしまうケースなどもあります。
ピッキング作業のミス
ピッキング作業のミスにより誤納品・誤出荷が起きるケースでは、以下のような原因が挙げられます。
・誤った製品や部品の選定:
製品ラベルや品番が似ている場合、誤って別のモノをピッキングしてしまうことがあります。
・数量の間違い:
出荷指示と異なる数をピックしてしまうミスです。例えば、10個の指示に対して9個ピックしてしまうようなケースがあります。
・ラベルやバーコードの誤り:
ピッキングの対象物のラベルが不鮮明な場合や、記載されている情報に誤りがある場合、ピッキングミスが発生しやすくなります。
・倉庫内の配置ミス:
製品が適切な場所に配置されていないと、作業員が正しいモノを見つけるのが難しくなり、ミスが発生しやすくなります。
発送時のミス
発送直前の最終確認が不十分な場合、誤った種類や数量が発送されてしまう可能性が高まります。
発送ラベルを誤って別のモノに貼ってしまう場合や、手書き伝票を誤って記入した場合、複数の注文をまとめて発送する場合などにミスが起きやすく、異なる顧客に製品や部品が届いてしまうケースがあります。
こうした誤納品・誤出荷の原因は、各工程におけるヒューマンエラーや管理の不備に起因するものが大半です。
誤納品・誤出荷による影響
誤納品・誤出荷が発生すると以下のような影響が生じます。
在庫に差異が発生する
誤納品・誤出荷が発生すると、データ上の在庫数と実際の在庫数に差異が生じます。
そのために、「いつ」「どこで」差異が生じたのか原因を追究する、データを修正するなどの無駄な手間がかかります。
また差異が発生すると、正確な在庫計画を立てにくくなり、欠品や過剰在庫のリスクが高まり、在庫管理費用の増加や機会損失の発生にもつながりかねません。
無駄なコストが発生する
誤納品・誤出荷はさまざまな面でコストの増加につながります。
例えば返品対応や再配送の手間が増え、人件費が上昇するほか、返品・正しい製品を再出荷するための配送費も余計にかかります。通常業務以外の作業が発生し、作業効率が低下することも人件費上昇の一因です。
こうした費用の増加を防ぐには情物一致を行うことが重要です。詳しくは以下記事をご覧ください。
信頼の低下を招く
誤納品・誤出荷が頻繁に発生すると取引先や顧客からの信頼が低下し、発注先を他社に切り替えられてしまう可能性があります。リードタイムが厳しい取引では、ビジネス機会の損失につながりやすいため特に注意が必要です。また、自社ブランドのイメージが低下し、将来的な取引減少のような長期的悪影響を及ぼす可能性もあります。
納品・出荷先を間違えた場合、第三者に個人情報が漏洩するリスクも生じます。
誤納品・誤出荷を防ぐ対策
誤納品・誤出荷を防ぐ対策としては以下の3つがあります。
業務フローをマニュアル化する
業務フローをマニュアル化して手順を明確にし、誰でも一定の品質で業務を遂行できるようにすることが重要です。棚に保管する際のロケーション管理のルールや、ダブルチェックの徹底といった対策もマニュアルに記載し、ミスの発生を抑えます。
マニュアル化することで新入社員や異動者に対して効率的に教育を行えるため、教育コストも抑制できます。
十分な作業スペースを確保する
作業スペースを十分に確保できていないと、さまざまなモノや梱包材、納品書などが狭いエリア内に混在してしまい、梱包や出荷の際にミスが生じやすくなります。十分な作業スペースがあることで、従業員は必要なモノを正確かつ迅速にピッキングできるようになり、誤納品・誤出荷のリスクが低下します。
システムを導入する
人の手による作業の割合が大きい場合は、システムの導入が特に効果的です。
例えば在庫管理システム(WMS)を導入することで、リアルタイムで在庫状況を把握できるようになり、誤納品・誤出荷や在庫差異を防ぎやすくなります。
またRFIDを導入すれば、一度の複数の製品の情報を読み取れ、システム上で確認作業が行えるので、人為的なミスの低減や業務効率化に寄与します。
誤納品・誤出荷を防ぐシステム
誤納品・誤出荷は、在庫管理の混乱、コスト増加、ブランドイメージ・信頼の低下など多方面にわたり悪影響を及ぼすため、マニュアル化や作業スペースの確保、システムの導入などにより防ぐことが重要です。
小林クリエイトでは、誤納品・誤出荷を防ぐシステムとして「ハブリッジシステム」を提供しています。ハンディーターミナルを活用し、製品出荷時の現品票差し替えチェック、製品入出庫置き場のチェックなど、都度出荷データと照合し作業を進めることが可能です。
前述した在庫管理システム(WMS)は、パッケージ型の場合初期費用が300~1000万円ほどかかってしまいますが、ハブリッジシステムの場合、現品票はそのままでバーコードやQRコードを設定するため、開発コストを抑えられます。
誤品照合以外でも、工程内のモノの移動管理や作業実績の収集など、さまざまなシチュエーションで活用いただけます。
サービスの詳細は以下の資料をご覧ください。
お役立ち資料はこちら
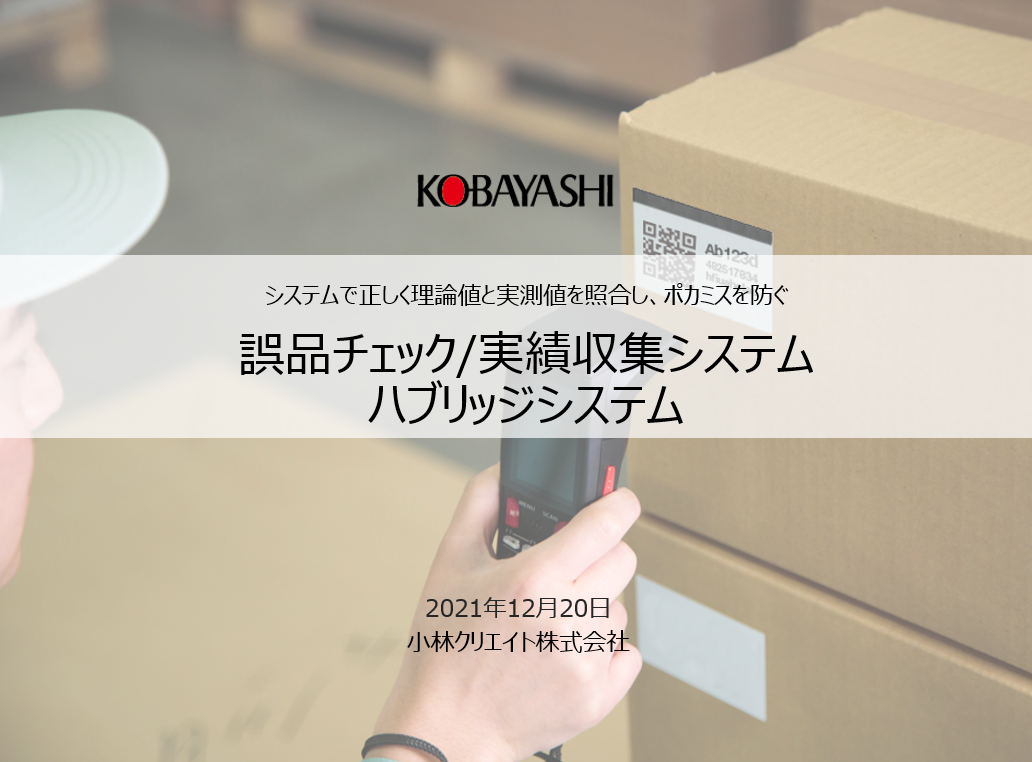
お役立ち資料
システム
「ハブリッジシステム」

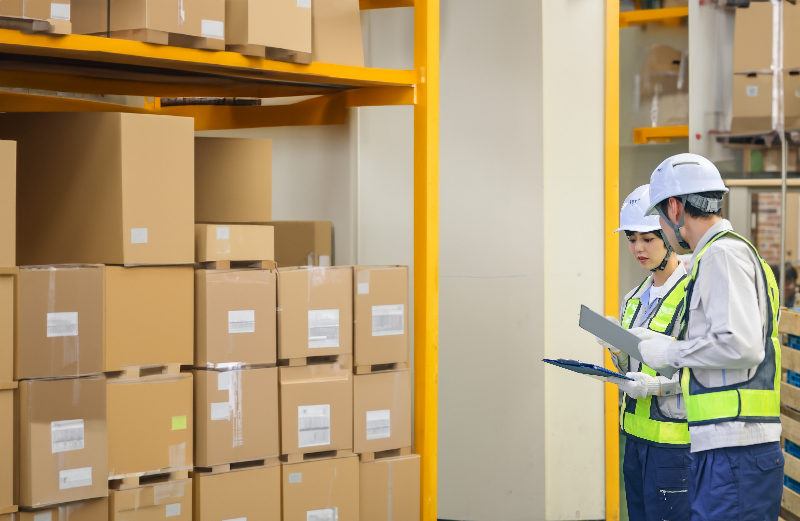
対策とは?
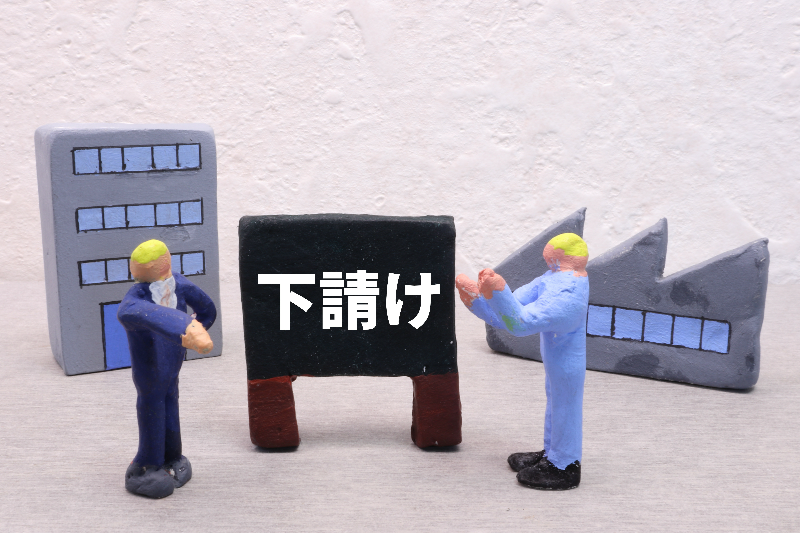
適切に行うポイントとは?
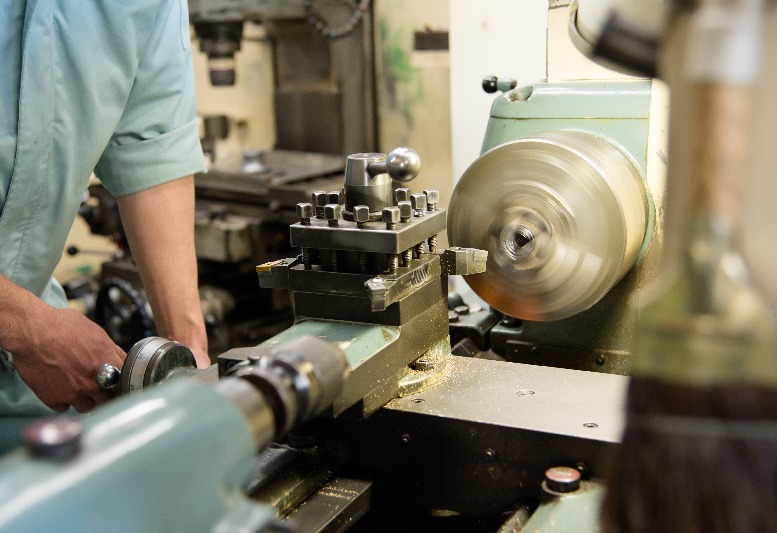
業務効率化の方法と事例を紹介