適正在庫の考え方と計算方法、
在庫最適化の実現方法を紹介
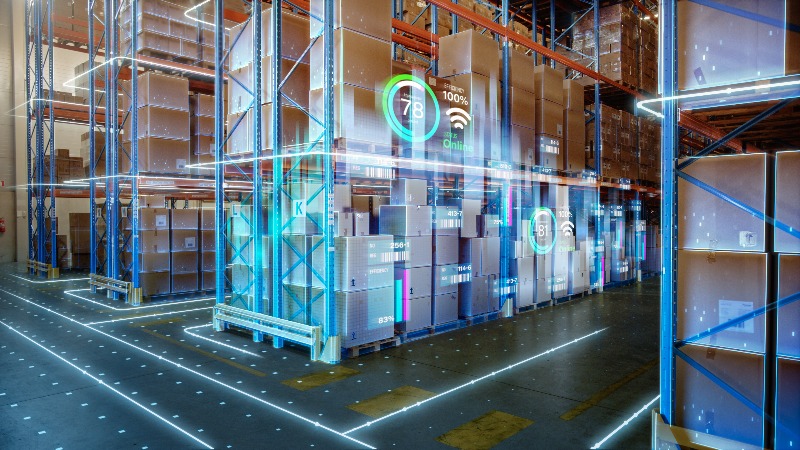
製造業の現場では、適正在庫をいかに実現するかが課題となっています。適正在庫を実現することで、収益性の改善やリードタイムの短縮が可能になるなど、さまざまなメリットを得られます。しかし、適正在庫とは具体的にどのようなもので、どう実現すれば良いかわからない方もいるのではないでしょうか。本記事では、適正在庫の考え方や実現できていないことのリスク、在庫最適化の方法などをご紹介します。

適正在庫とは?安全在庫との違い
適正在庫とは、欠品が生じず、過剰な在庫も発生しない在庫数量のことです。適正在庫は正確な需要予測によって実現でき、在庫の過不足を解消し機会損失を防ぎます。また、キャッシュフローが最適化し、利益の最大化にもつながります。
適正在庫と似た概念に安全在庫があります。安全在庫は、需要が変動しても欠品が生じない在庫数量のことであり、在庫の下限としての意味合いがあります。一方で、適正在庫は下限だけでなく、過剰在庫を発生させないよう上限の数量も設定します。
過剰在庫や欠品…在庫最適化の重要性とできていないことのリスク
物流や製造の現場では、在庫をいかに適切に管理するかが問われるため、在庫最適化を行うことが重要です。在庫最適化ができていないことによるリスクとしては、主に以下の6つがあります。
リスク①:収益性の低下
過剰在庫が発生していると、在庫をさばくために廉価販売しなければならない可能性があり、それでも販売しきれなかった在庫は破棄することになります。その場合、利益が縮小するばかりか仕入原価さえ回収できない可能性もあり、収益性の低下は避けられません。また、在庫が過少な場合も需要を満たせずに機会損失が発生し、収益が悪化します。
リスク②:作業工数の増加
過剰在庫が存在すると、販売店から倉庫への返品や破棄のための作業が必要になり、余計な工数が発生します。在庫が過少な場合も、倉庫と工場間などで頻繁に在庫を出し入れすることになり、工数が増加します。こうした工数は付加価値を生まず、業務効率の低下を招いてしまいます。
リスク③:製品の品質劣化
多くの製品は、品質保証期間を経過すると品質低下が進みやすくなります。また、劣化はしなくても技術やトレンドなどの変化により時代遅れとなることも珍しくありません。そうなると商品価値は低下し、需要が減るために廉価販売や破棄を余儀なくされることがあります。
リスク④:キャッシュフローの悪化
前述の通り、廉価販売や在庫の破棄は収益性を低下させますが、それによりキャッシュフローが悪化することも大きなリスクです。在庫は資産ではあるものの、現金とは違い流動性が低いこともキャッシュフロー悪化の要因となります。キャッシュが減るために、他の分野への投資や運用もしにくくなります。
リスク⑤:保管コストの増加
在庫を過剰に抱えると多くの保管スペースが必要となり、場合によっては新たな倉庫など追加の保管スペースを確保しなければなりません。その場合、倉庫の賃料や人件費などの保管コストが増加します。また、在庫を棚に置ききれず通路や床に置くようになると、管理が煩雑になり入出庫に余計な時間をかけることにもなります。
リスク⑥:リードタイムの長期化
適正在庫を実現していれば、必要なときに必要な量だけを出荷でき、リードタイムを最短化しやすくなります。しかし、在庫が足りないと需要が増えたときに製品の入荷を待たなければならず、結果としてリードタイムが長くなる課題があります。過剰在庫を抱えている場合も、前述のように管理が煩雑になり、余計な工程が増えることでリードタイムが長期化する可能性があります。
これらのリスクを回避するために、適正在庫の考え方は非常に重要です。では実際に、適正在庫をどのように求めれば良いのでしょうか。次章で解説します。
適正在庫の求め方(計算式)
適正在庫の代表的な求め方(計算式)は主に以下の4つがあります。
・「安全在庫+サイクル在庫」
適正在庫の計算方法の中でも基本的なものです。サイクル在庫は、発注と発注の間で消費する在庫量の2分の1の数量を意味します。
安全在庫は以下の計算式で算出します。
安全在庫=安全係数(1.65※)×使用量の標準偏差×√(発注リードタイム+発注間隔)
※安全係数は欠品許容率のことであり、欠品許容率5%にあたる1.65とする。
・「一定期間の需要数+安全在庫」(需要数からの求め方)
一定期間における需要数と安全在庫の合計から求める方法です。需要が比較的安定した製品を扱う場合に適しています。
・「在庫回転率÷在庫回転日数」
経営視点から適正在庫を把握したい場合に適した計算方法です。
在庫回転率は「年間もしくは月間の売上原価 ÷ 平均在庫金額」で求められ、在庫回転日数は「日数 ÷ 在庫回転率」で測ります。
・「売上目標÷在庫回転率」(交叉比率からの求め方)
交叉比率は、「その在庫でどれだけの利益が上がっているか」を示す指標であり、「在庫回転率 × 粗利率」で求められます。
上の式を変形して在庫回転率を求めることもでき(交叉比率 ÷ 粗利率)、売上目標を在庫回転率で割ることで適正在庫金額を計算できます。
製造業における在庫管理の方法やポイントなどについてはこちらの記事で解説していますので、あわせてご覧ください。
本章では適正在庫の求め方を紹介しましたが、次章では適正在庫を維持する方法について解説します。
適正在庫を維持する方法
適正在庫を維持するためには、全社的に適正在庫の数量を統一し、発注方法の見直しや需給予測の精度向上などを行うことが必要です。
会社全体で適正在庫を統一する
部門によって適正在庫の捉え方が異なると、適正在庫の実現は困難です。例えば、倉庫を管理する部門は保管コストを抑えるため適正在庫を少なめに見積もる一方、販売部門は急な発注の増加にも対応できるように多めの在庫量を見積もる、といった事態が考えられます。
各部門がコミュニケーションをしっかりととり、会社全体で最適な在庫の数量がどのくらいなのかコンセンサスを得ることが重要です。
発注方法の見直し
発注方法には簡易発注方式、不定量不定期発注方式、同期化発注方式、分納発注方式などさまざまなものがありますが、大きく分けると定期発注方式と定量発注方式があり、現状の発注方法が非効率であれば見直す必要があります。
定期発注方式は、「1週間に1度」や「毎月10日」といったように、時期を決めて発注する方式です。発注量は毎回変わっても問題なく、必要な量を発注できるので、時期によって需要変動が大きい製品に適しています。
一方、定量発注方式はあらかじめ発注する量を定めておき、在庫が一定量まで減ったときに決められた量を発注する方式です。定量発注方式は発注する量が毎回同じなので、需要予測が不要ですが、急な需要の増減には対応しにくい特徴があります。そのため、基本的には発注量の変化が比較的少ない製品に向いています。
両者の発注方法の特徴はほぼ正反対であり、どちらの方が優れているというわけではありません。違いを理解した上で最適なものを選ぶことが重要です。
需給予測の精度を上げる
需要予測の精度を上げることも大切です。適正在庫の数量を正確に把握することはもちろん、季節ごとで需要の増減の傾向や月ごとの販売数量・発注履歴といった過去のデータ、さらにトレンドの変化なども踏まえて最適な在庫数量を試算します。
予測の精度を上げるためには、従業員の勘と属人性に頼るのではなく、システムを導入することが効果的でしょう。
サプライチェーンの改善(リードタイムの短縮)
生産から販売までの一貫した流れであるサプライチェーンを改善することでリードタイムを短縮し、必要なときに必要な在庫をすぐに供給できる体制を構築することも重要です。
例えば、サプライヤーと需要予測の結果などを密に情報共有し、スムーズに納入してもらえるような関係性を構築することや、製造工程における無駄の排除、不良品発生率の低減といった施策を進めると良いでしょう。
在庫の「みえる化」(リアルタイムの情報管理)
現状の在庫数量を正確に把握する「みえる化」を進めることも、適正在庫の実現のために必要な施策です。現状の在庫をみえる化することで適正在庫との差分を把握でき、需要の増減に応じて製品を適宜補充・調達したり削減したりでき、適切に在庫数量を調整しやすくなります。
また、適正在庫と現状の在庫の差をリアルタイムで把握し、情報管理することで、現状の在庫管理の課題を洗い出し、適切な改善策を講じることもできます。
在庫の最適化を実現するソリューション
前述のような在庫の「みえる化」を実現する方法として、RFタグを活用した在庫管理のソリューションがあります。
まず、製品の入庫時にRFタグを利用し、入庫情報とタグ情報を紐づけます。出庫時や棚卸時には、製品についたRFタグを専用のリーダーで読取することで、在庫情報を更新することが可能です。これによりヒューマンエラーを削減でき、効率的な在庫管理を実現します。
さらに、読み取った情報をシステムで一元管理することにより、在庫を「みえる化」し、在庫の過不足解消(適正在庫の実現)につなげることも可能です。
以下の資料ではRFタグを活用した製造現場改善アイデアをご紹介していますので、ぜひご覧ください。
お役立ち資料はこちら
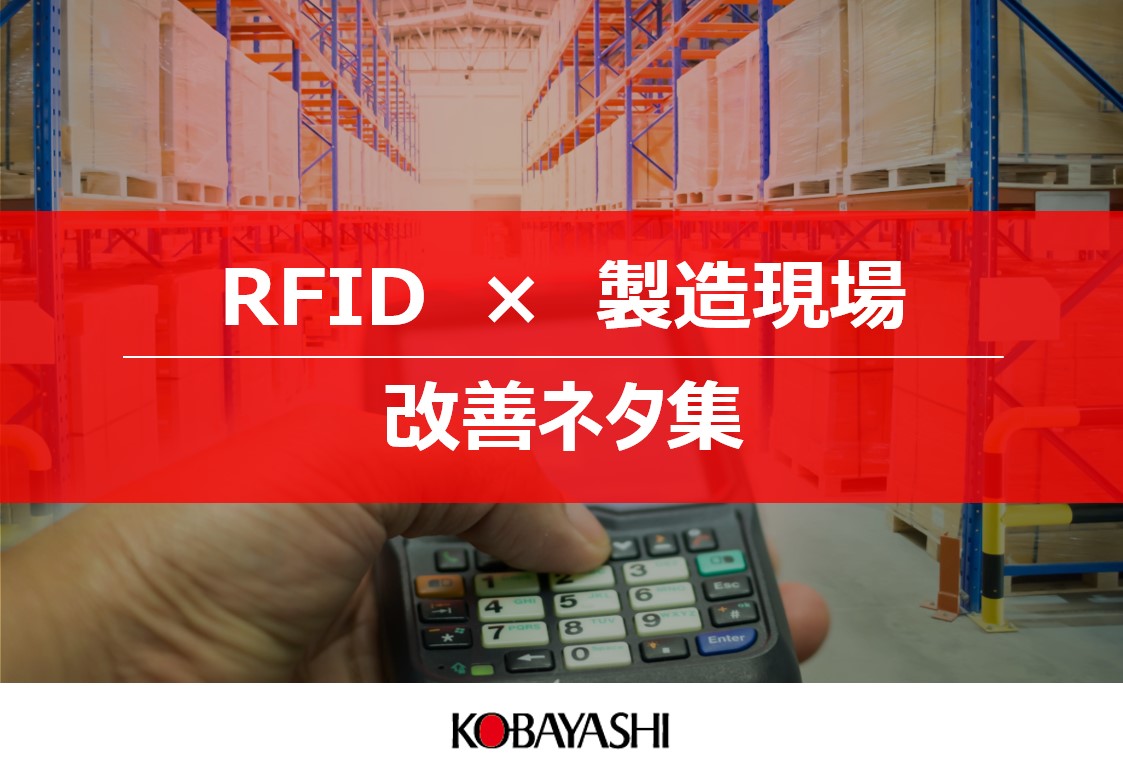
お役立ち資料
改善ネタ集
