現場担当者必見!
製造業における生産性向上に向けた改善事例をご紹介
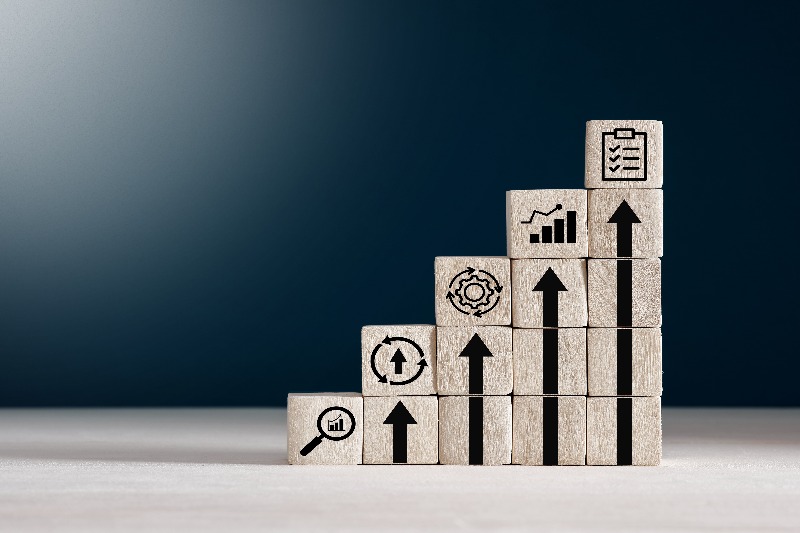
製造現場の生産性向上を図りたいものの、思ったように進んでいない、何をすればいいのかわからないというは多いのではないでしょうか。生産性向上は製造現場における課題の1つですが、なかなか改善に取り組めていないケースも少なくありません。本記事では、製造現場で生産性向上を妨げる要因や生産性向上を実現した具体的な事例などをご紹介します。

製造現場における生産性の向上を妨げる
3つの要因
製造現場では、労働人口の減少や製品の競争激化などの背景から、品質を担保しつつ、より効率的な生産を行うことが求められています。
生産性向上のためには、従業員1人当たりの生産量の増加や手順・作業における無駄な時間の低減などの方法が挙げられます。実際の製造現場では、以下3つの要因があり、なかなか進められていないのが現状です。
作業の標準化ができていない
1つ目の要因は、作業の標準化がされていないことです。
生産性向上のためには、1人当たりの生産効率が重要であり、誰でも同じレベルのパフォーマンスを発揮する必要があります。しかし、多くの製造現場は、作業内容が標準化されていないために、ベテランと新人の生産量や品質に差が生まれ、生産性向上につながりにくい状況となっています。
このような状況ではノウハウもなかなか蓄積されないため、新人が育たず、ベテランが離職してしまった場合に、生産性が大きく低下してしまう恐れがあります。
ヒューマンエラーによるムダの発生
2つ目は、従業員の作業ミスといったヒューマンエラーによる生産性の低下です。
製造工程において、作業ミスのような意図しないエラーが発生することで、その対応による無駄な時間が生まれます。また、ヒューマンエラーの発生は原料や素材の量に対して生産された完成品の割合である歩留まり率の低下を起こす原因でもあります
このようなヒューマンエラーの対策として、現場では従業員によるダブルチェックがよく行われていますが、チェック作業に費やす時間が増えてしまっていることから、生産性の低下を起こしています。
製造業のヒューマンエラーについては以下記事でも解説しております。
部品調達や在庫管理の状況が不透明
製造現場において、各工程を滞りなく進めるためには、不足の無い部品調達と、その部品の在庫管理状況の把握が重要です。
しかし、多くの現場では、この部品調達や在庫管理の状況が不透明であり、把握できていません。このような状況では、必要な部品がなかったり、部品を探す時間がかかったりするため、製造工程に遅れが発生し、生産性向上の妨げとなります。
在庫管理では、データ上の情報と実際のモノの状況が一致している「情物一致」の状態が理想的です。情物一致については以下の記事で解説しております。
生産フロー別!製造業における現場改善事例
前章で紹介したような要因を解決し、生産性向上を実現するために、製造現場ではさまざまな改善が行われています。以降では、どのような改善事例があるのかを在庫管理・出荷・部品調達管理の3つのケースにて紹介します。
事例①:在庫管理
1つ目が、適切な在庫管理を行うことで生産性向上を図った事例です。
ある製造会社では、製品の材料として、ゴム原材料と薬品を混合したゴム材料を倉庫で一時管理しており、そのゴム材料は種類によって使用期限を管理する必要がありました。実際の現場では、ゴム材料の運搬・管理を運用者の属人性に頼っており、先入れ先出しが徹底できず、使用期限の切れた材料を破棄するムダが発生していました。
そこで、自動認識技術であるRFIDを導入しています。
ゴム材料に使用期限の情報 が書き込みされたRFタグを取り付けることで、材料それぞれの使用期限管理ができるようになりました。さらに、誤った材料を持ち出してしまった場合は、信号灯などで警告を発することにより、先入れ先出しが徹底されるようになりました。
結果、適切な在庫管理が行われ、使用期限切れのゴム材料の発生の防止による材料廃棄の低減を実現しています。
このような自動認識技術RFIDを活用したソリューションについては以下をご覧ください。
RFIDを活用した在庫管理の最適化については以下記事でも解説しております。あわせてご覧ください。
事例②:出荷
2つ目が、出荷業務の改善による生産性向上を行った事例です。
ある企業では、出荷時に、客先現品票と社内現品票の差し替え間違いによる誤出荷が発生していました。また、出荷業務はいまだに人手によって頼っている部分も多く、ヒューマンエラーの頻発が問題となっていました。
そこで、集荷指示書を二次元コードで読み取り、客先現品票と社内現品票を差し替える際の3点照合を実施しました。
結果、製品出荷時の現品票差し替えチェック、製品入出庫置き場のチェックなど、その都度出荷データと照合し作業が進められるようになり、ヒューマンエラーによる誤出荷リスクを低減しています。
本事例で導入されたソリューションは以下になります。ご興味のある方はぜひご覧ください。
事例③:部品調達管理
3つ目が、部品調達管理の体制改善による生産性向上を行った事例です。
ある企業では、部品調達や在庫管理状況が不透明であり、製品の過剰在庫や欠品などが発生している状況でした。
そこで、かんばん方式を採用した部品調達のシステム化・データ化を実施しました。
かんばん方式とは、商品名・品番・保管場所などの情報が記載された「かんばん」を活用し、必要なものを必要な分だけ生産する管理方法のことです。このかんばん方式をシステム化・データ化することで、在庫低減やリードタイムの短縮を実現しています。
かんばん方式を採用した部品調達は以下ソリューションの導入によって実現可能です。ご興味のある方はぜひご覧ください。
製造現場に合わせた現場改善の提案なら
小林クリエイトにお任せ
小林クリエイトは、80余年の間、自動車関連業界をはじめとした製造業界全般で、業務効率化・コスト低減などに貢献してきたモノづくり現場の業務改善のスペシャリストです。
本記事でご紹介したような生産フロー別の現場改善に向けた支援を行っている他、現場改善のプロフェッショナルとしてサポートしてきたノウハウの活用による、顧客の現場に合わせた提案も可能です。
以下資料では、小林クリエイトが提供するIoT技術を活用した現場改善事例についてご紹介しています。ご興味のある方はぜひご覧ください。
お役立ち資料はこちら
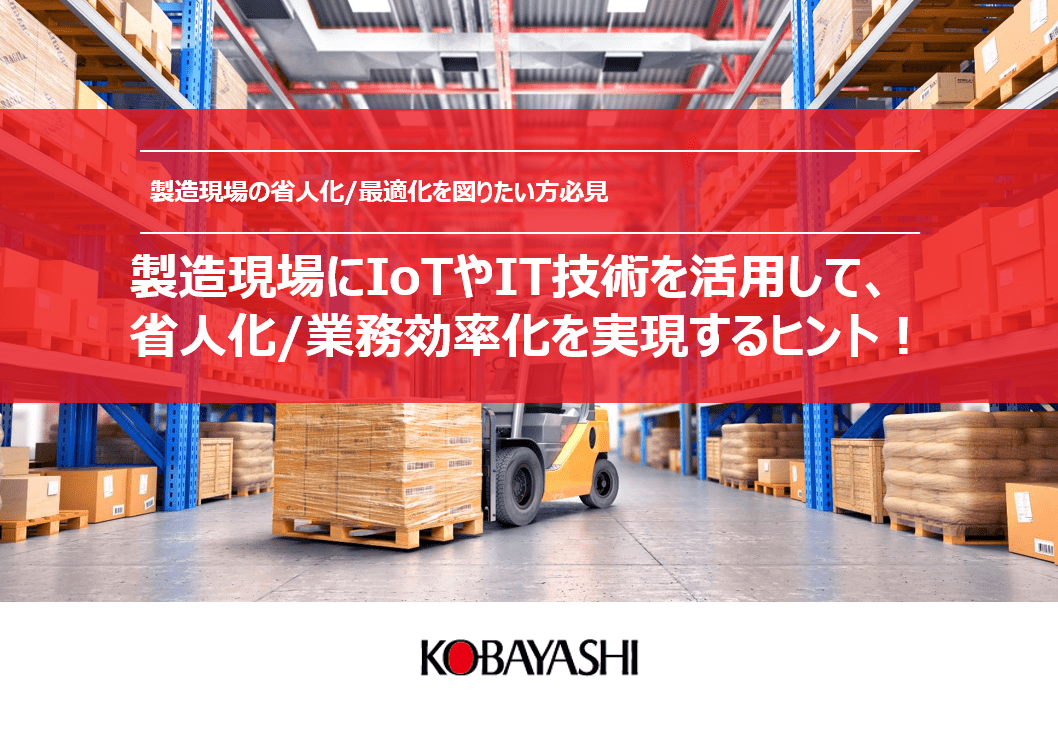
お役立ち資料
省人化/業務効率化を実現するヒント!

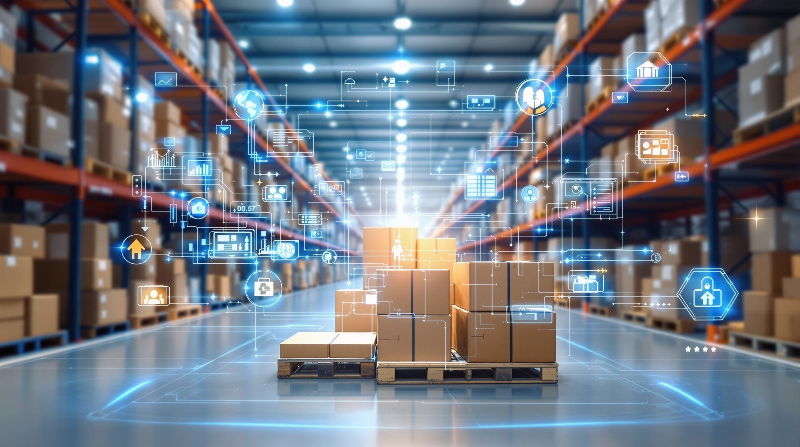
業務内容や効率化する方法を解説
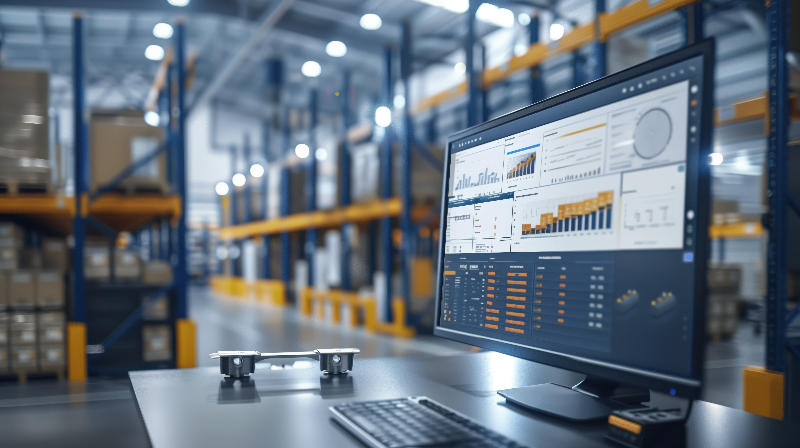
課題と解決策を解説
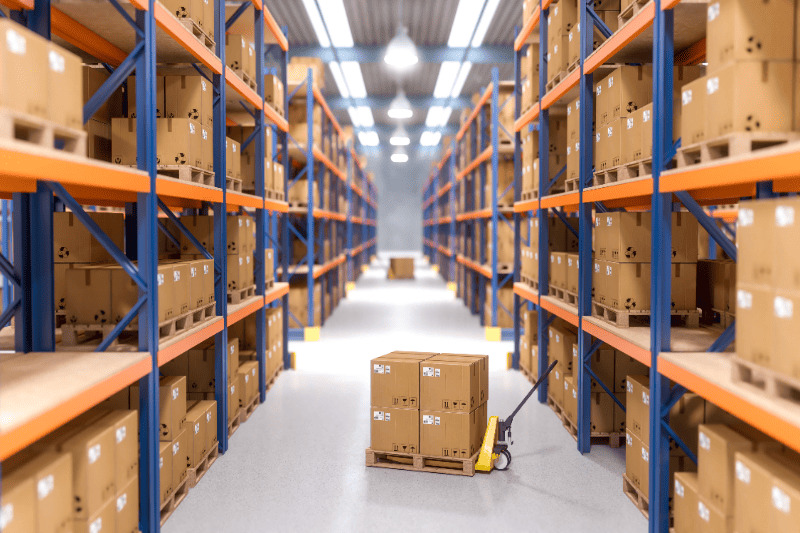
よくある課題、効率化する方法を解説