工場が取り組むべき省力化とは?
省人化との違い、IT/IoT活用による事例を紹介
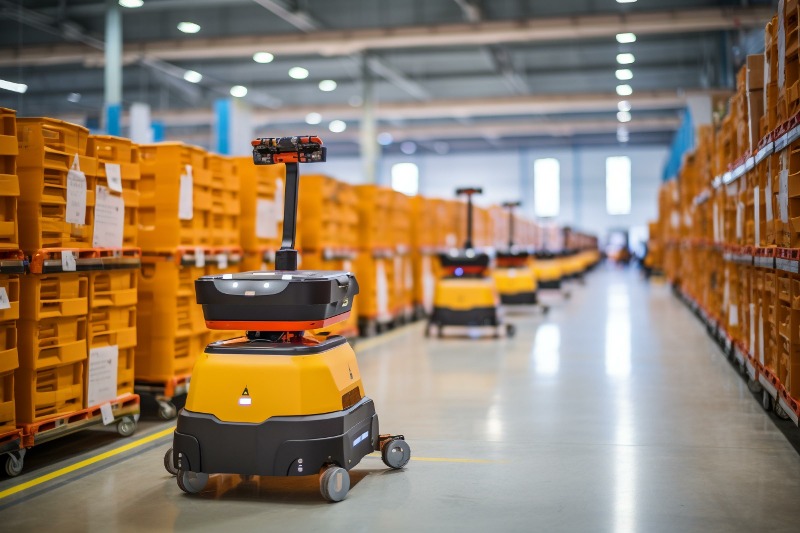
人手不足が進む工場の現場では、少ない労力で高い生産性を実現する省力化の重要性が増しています。省力化を進めることで人手不足を緩和でき、生産性向上や作業環境改善といったメリットを得られます。本記事では、工場の現場で省力化を進める方法やIT/IoTを活用した省力化の事例などをご紹介します。

工場の省力化とは
まずは、工場の現場で注目される省力化とはどのようなものなのかについて解説します。
省力化の意味
省力化とは、人が行う工程の無駄を省き、作業量・業務量を削減することです。これまで人が行っていた作業の無駄を削減することで、効率的な業務を実現し、従業員の負担を軽減します。
省人化/少人化との違い
省力化と類似の概念に、省人化や少人化(しょうにんか)があります。省人化は人員削減に重きを置くのに対し、省力化は手間や労力の軽減に注力するものです(実際に人員を削減したかどうかは問いません)。
また、少人化は需要の変動に合わせて必要な人員を増減させることです。常に最小の人数で生産ライン運営などの業務をこなし、生産に10人必要なときは10人で、5人で対応できるときは5人で対応します。
省力化によって人が行う作業を見直し、無駄を省くことで、生産性向上につながります。省力化は、将来的な省人化に向けた前段階のプロセスともいえるでしょう。
工場が省力化に取り組むべき理由
人が行う作業の無駄を省き、業務効率化や生産性向上を図る省力化ですが、工場が省力化に取り組むべき理由として以下の3つがあります。
人手不足の緩和
少子高齢化の影響で製造業の現場では人手不足が進んでおり、数多くの従業員を確保することが難しくなっています。また、働き方改革を背景に長時間労働の是正も求められており、人的資源はますます限られてきている状況です。
省力化を進めることで全体の業務量を削減でき、限られた人的資源でも成果を維持・拡大できるようになるため、人手不足を緩和できます。
製造業の人手不足の理由については、こちらの記事で詳しく解説しています。
生産性の向上
省力化を進める際に、新たな機械やシステムを導入することで大幅な生産性向上が期待できます。また、省力化により無駄な業務が減れば、人件費を抑えながら生産量を維持できるため、利益の向上につながります。
以下の記事では、製造現場で生産性を向上する取り組みについて解説していますので、併せてご覧ください。
作業環境の改善
省力化の過程で人が行う作業を減らすことで、事故が発生するリスクを減らすことも可能です。また、作業の効率化が進み業務量が減ることで、従業員の働き方に余裕ができることも作業環境の改善につながります。
本章では工場が省力化に取り組むべき理由を解説しましたが、実際にどのような方法で進めたら良いのでしょうか。次章で説明します。
省力化を進める方法
省力化を進める際には、以下の5つのプロセスを踏む必要があります。
①既存業務の整理
まずは既存業務を整理し、負担の大きな業務や多くの人的資源を割いている業務を洗い出します。そうすることで、現状の設備や人的資源で省力化を実現できる可能性があります。一つひとつの工程を細分化し、各工程でかかっている負荷や業務時間、人員などを把握できるようにすることがポイントです。
②作業量や作業工程の見直し・改善
①で既存業務を整理したら、作業量や作業工程を見直し、無駄な工程が発生していないかチェックします。人手を使わなくても良い業務や非効率な業務は、効率化に向けた改善を進めることで省力化につながります。
③作業の標準化・マニュアル化
次に、担当者ごとの手順や道具の使い方の違いなどを把握し、最も効率的なやり方に標準化します。各工程の作業が標準化されていないと、従業員の熟練度によって生産性が大きく変わり、属人化の原因にもなります。そのため、誰でもやり方を理解できるようマニュアル化することも重要です。
④現場への周知・従業員の教育
③を実施した後には、従業員へのマニュアルの配布や研修の実施を行い、現場に周知します。なぜ省力化を実施するのか、どのような変化が期待されるのかを明確に伝え、従業員とのコミュニケーションを図ることがポイントです。これらを通じて、従業員が新しい作業内容に適応できるように十分に教育します。
⑤IT・IoT導入による効率化
IT・IoT技術を活用したソリューションを導入することで、人が行うべき業務を自動化できます。既存業務の見直し・改善や標準化などだけでは限界があるため、この方法は省力化に向けた抜本的な改善につながります。なお、IT・IoTの導入にはコストがかかるため、中長期的な費用対効果を試算しておくことがポイントです。
省力化を進めるには以上の5つのプロセスを踏むことが重要ですが、次章では実際に省力化した事例を解説します。
製造業の省力化事例
以下では、IT/IoT技術を活用し省力化した事例を、製造業向けにシステムを提供している小林クリエイトの実際の導入事例をもとに、4つご紹介します。
事例① 通い箱・パレット管理システム活用による省力化
通い箱・パレット管理では、他社のものと自社のものの見分けがつかなくなる可能性や、他社が誤って持ち帰ってしまうことで所在がわからなくなる可能性があります。その場合、所有者の特定や返却手続きに余計な手間が発生し、現場の業務効率や生産性の低下につながってしまいます。
通い箱・パレットなどの循環輸送資材の管理状況を「みえる化」してくれるパッケージシステム「RePaX」を活用し、RFタグの付与によりID管理することで、何の資材がいつ、どこに出荷され、どのくらいあるのかを正確に把握・管理することが可能です。
事例② 治具・工具管理システム導入による省力化
治具・工具の持ち出し管理ができていないと、工具の所在がわからず、その探索に多くの時間がかかってしまいます。持ち出し管理をする場合、持ち出し/返却時の台帳記入が手間になり、記入の抜け漏れなどが発生することも課題です。
そこで備品管理のソリューション「ぶっぴんさん」を活用し、RFタグや二次元コードを備品に取り付けることで、備品の所在管理を簡単に実現できます。
事例③ 金型管理システム導入による省力化
金型管理においては、ショット数の管理ができていなかったり、金型メンテナンスのタイミングを把握できていなかったりするケースがよくあり、多くの現場で省力化を阻む課題となっています。
RFタグを用いた金型管理システム「ぶっぴんさんfor金型」を活用すれば、RFタグを読み取ることで金型管理をシステム化でき、PCやタブレットで手軽に金型の貸し出し状況や置き場を確認することが可能です。ショット数は携帯端末に入力することにより、データ化されるため、業務効率化に貢献します。
事例④ 音声認識入力システムの導入による省力化
ピッキング作業では、日付や数量などを記録する必要があり、読み取り端末の取り出しやスキャンをする際に手がふさがることで、業務効率が落ちる問題があります。手書きした情報をパソコンに手入力する手間もかかり、その際にミスが発生することも少なくありません。
「音声認識入力システム」を導入することで、ピッキングに伴う入力作業をハンズフリーで行えるようになります。加えて、リストと製品の目視による照合もアイズフリーで行えるため、業務効率化を実現します。
ご紹介したもの以外にも、IT/IoTを活用して業務効率化や省力化を実現できる方法はさまざまにあります。以下の資料では、そうした省人化/業務効率化を実現するヒントを解説していますので、ぜひご覧ください。
お役立ち資料はこちら
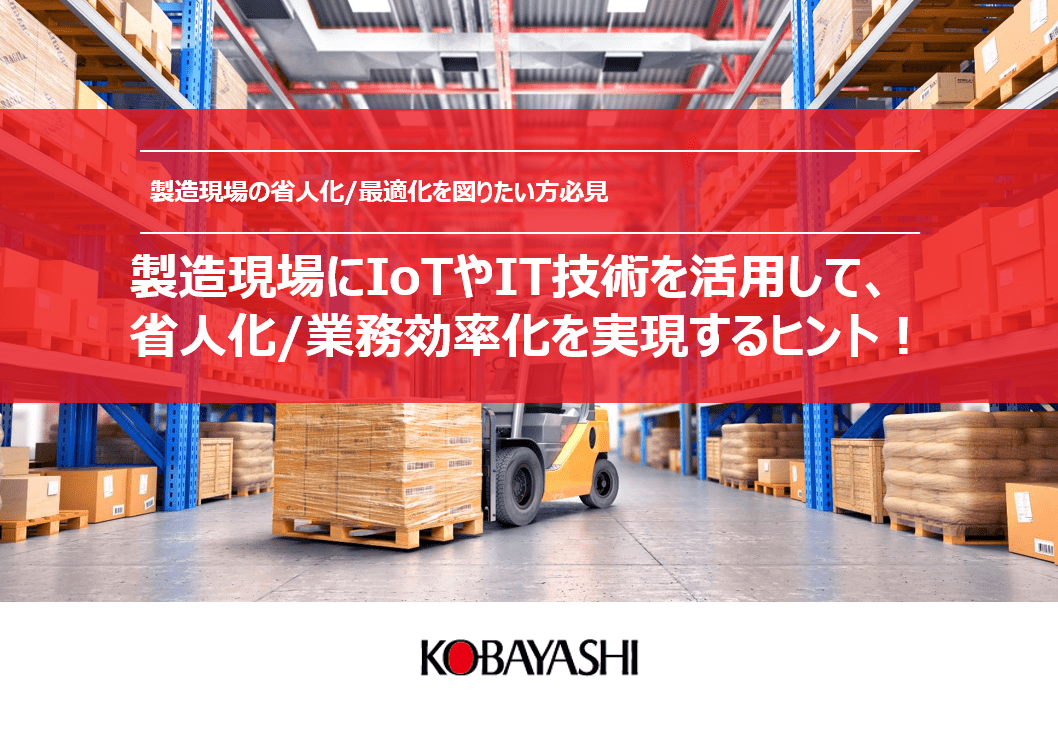
お役立ち資料
省人化/業務効率化を実現するヒント!

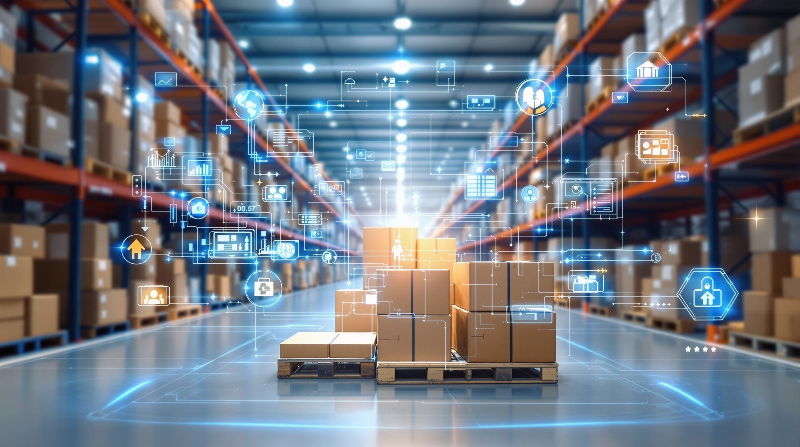
業務内容や効率化する方法を解説
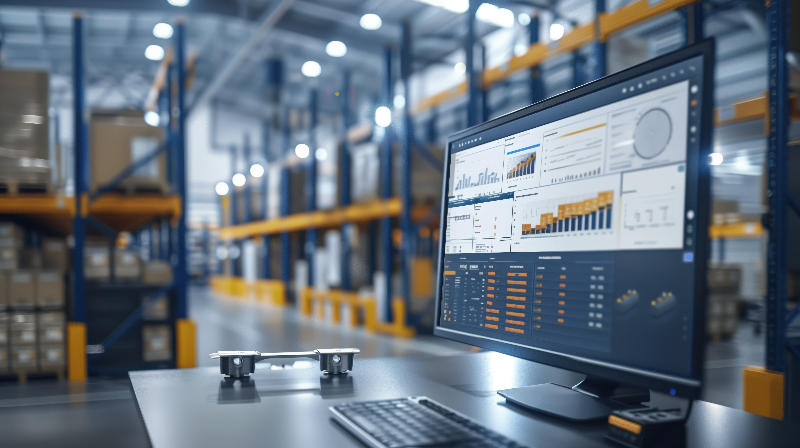
課題と解決策を解説
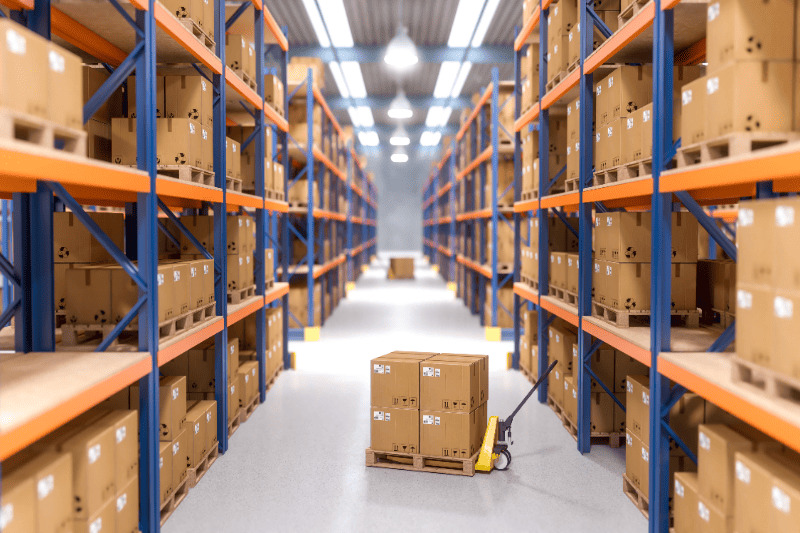
よくある課題、効率化する方法を解説