【事例付き】ピッキング作業を改善する方法!
よくある課題と効率化のポイント
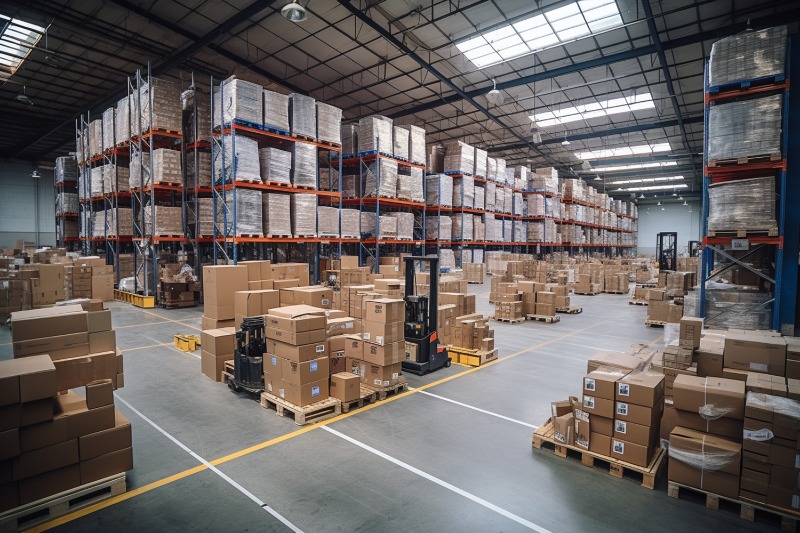
物流現場のピッキング作業では、手作業や目視での照合によるピッキングミスの発生や、作業に時間がかかるといった課題があります。そうした課題については、ロケーションの改善やピッキングリストの工夫などの対策が有効であり、より抜本的な対策としてはピッキングシステムの導入が重要になります。本記事では、ピッキング作業を効率化する方法について、ポイントと具体的な事例も含めて詳しくご紹介します。

ピッキング作業でよくある課題
物流現場ではスムーズな出荷を実現するために、指定の製品を取り出して集めるピッキングが重要です。しかし、ピッキング作業には以下のような課題があります。
ピッキングミスの発生
指示書を基に手作業・目視でピッキング作業を行う場合、品番の異なる製品や類似の製品を誤ってピッキングしたり、数量の間違いが起きたりするなどのヒューマンエラーが発生しやすくなります。ベテランの作業員と比較すると、経験が少ない新人の作業員がこのようなミスを起こしてしまう傾向があります。
また、ピッキング作業の確認ミスによって在庫情報と現物の情報が一致しなくなり、在庫の過不足が生じる場合があることも課題です。
ピッキング作業に時間がかかる
リストの内容を目視で確認しながらピッキングする場合、リストに記載された保管場所の情報が不十分だと製品を探すことに時間がかかります。
製品がリストとは異なる場所に間違えて保管されていたり、見つけにくい場所に置かれていたりすると、さらに時間をロスしてしまいます。
また、倉庫が広いと倉庫内を移動するだけでも時間がかります。また、棚同士の間隔が狭く倉庫のレイアウトが移動に不便な場合も、ピッキング作業時間の増加につながるため注意が必要です。
ピッキング作業に限らず、出荷業務全般の課題やムダを省くヒントについては以下の記事で詳しく解説しています。
また、ピッキング作業と同様に物流で重要な工程である棚卸の課題と効率化のポイントについては、以下の記事で詳しく解説しています。
こうしたピッキング作業の課題を解消し、業務効率化を図るにはどうすれば良いのでしょうか。次章では、ピッキング作業を効率化するための3つのポイントをご紹介します。
ピッキング作業を効率化するポイント
ピッキング作業を効率化するためには、以下のポイントを押さえる必要があります。
ロケーションの改善
まずは、倉庫内の製品を保管する位置や棚のレイアウトといったロケーションの改善が重要です。
頻繁にピッキングする製品を取り出しやすい手前に置いたり、棚に番号を割り振ったりすることで、どこに何があるのかを把握しやすくして製品を探す時間を短縮します。
また、棚同士の距離を十分に空けてレイアウトを変えることで、作業者が移動しやすい環境を整えることも効果的です。
ピッキングリストの工夫
次に、ピッキングリストに記載する項目を精査し、作業者が一目で必要な情報を確認できるようにする工夫が必要です。
ピッキングリストは納品書と異なり、数量や品番、ロケーションなど、ピッキングに必要な情報のみが網羅されていれば問題ありません。その他の情報が多く載っていると作業者の確認ミスを誘発しやすいため、余分な確認項目がないかを整理しましょう。
ピッキングシステムの導入
上記の改善策を進めても、人が作業するうえでミスを完全になくすことは難しく、ピッキング時間の短縮にも限界があります。新人の場合は特に作業時間がかかり、ミスをなくすことも簡単ではありません。
そのような場合は、ピッキングシステムを導入し作業の効率化を進めることで、異なる製品をピッキングするなどのミスを防ぐことができます。また、業務の一部をシステムで自動化できるため、経験の浅いスタッフでも効率的な作業を実現することができます。
ピッキング作業の改善事例
前章でご紹介したピッキングシステムの具体例としては、バーコードや音声入力を活用したシステムがあります。以降では、これらを導入することでピッキング作業がどのように改善されるかを解説します。
バーコード/RFIDの活用によるピッキング作業の効率化
出荷伝票や納品書に記載されたバーコード/二次元コードをハンディターミナルで読み取るシステムを導入することで、目視に頼らずに自動で照合でき、品番の見間違いによるヒューマンエラーを低減できます。
小林クリエイトでは、ピッキング作業のミス防止や効率化に関連したソリューションとして、バーコード/二次元コードを用いた誤品チェック/実績収集システム「ハブリッジシステム」を扱っています。ハブリッジシステムでは、複数のバーコードの照合パターンが登録可能であり、取引先毎に読取システムを開発する必要がなく開発費を抑えることができます。ハブリッジシステムについては、以下より資料をご覧ください。
また、電波を使って非接触で情報を読み取るRFIDを導入することで、複数の製品を一括で読み取ることができ、ピッキング作業の業務効率化や作業時間の大幅な短縮を実現できます。
小林クリエイトでは、非接触での一括読み取りに対応したRFIDによる業務改善ソリューションのご提案が可能です。RFIDを活用した現場改善にご関心のある方は、以下よりお問合せください。
音声入力を活用した作業工数の低減
さらに、音声入力が可能なソリューションを導入することで、手入力による手間やミスを低減し、業務効率化を実現することができます。
通常のピッキング作業では、日付や数量などを手入力する必要があり、端末を取り出したりスキャンしたりする際に手がふさがってしまうため、業務効率が低下するという課題があります。また、手書きの情報をパソコンで手入力する際に手間がかかったり、転記ミスが発生したりすることも少なくありません。
そこに音声入力の技術を用いたソリューションを導入することで、ピッキング作業に伴う入力作業をハンズフリーで行うことができ、生産性向上・ミス低減が期待できます。
以下資料では、音声入力システムを導入したことで現場作業の生産性向上を実現した事例を紹介しています。
ピッキング作業を効率化して現場改善を
実現しよう
ピッキング作業の課題に対しては、まずはロケーションやリストの改善によって対処することが重要です。加えて、抜本的な解決策としてはピッキングシステムの導入が効果的です。特に、ご紹介したようなバーコード/RFIDや音声入力を活用したシステムを導入することで、ピッキングミスの低減や効率化を実現し、さらには現場作業員の省人化にもつながります。
ピッキングをはじめとする物流・製造現場の作業工数削減は、人手不足が進む中での喫緊の課題であるため、改善のアイデアを知っておくことが非常に重要です。以下資料では、製造現場の作業工数低減を実現する改善アイデアをまとめてご紹介しています。ご興味のある方はぜひご覧ください。
お役立ち資料はこちら
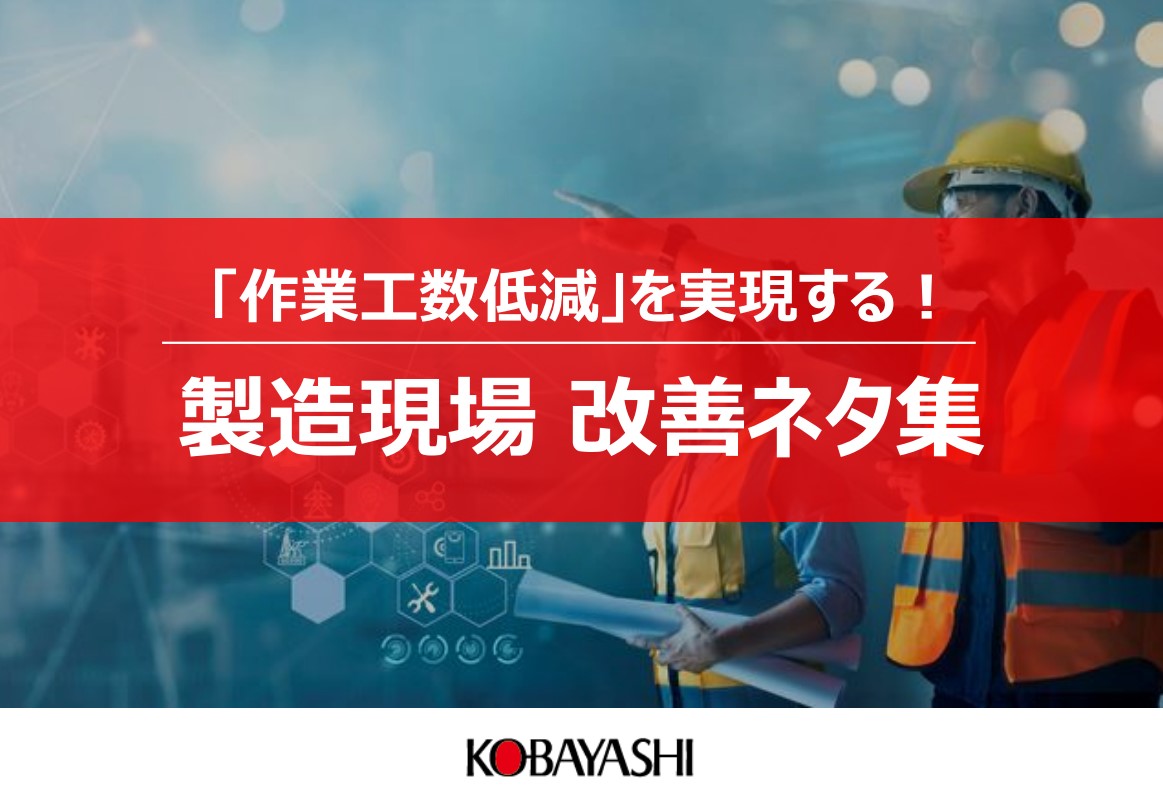
お役立ち資料

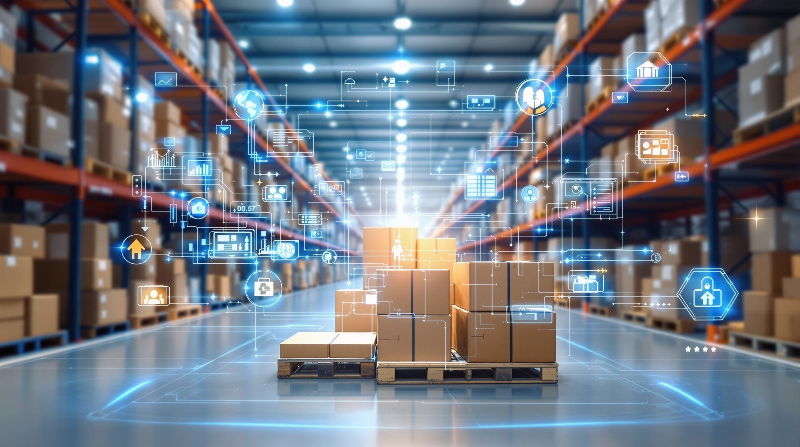
業務内容や効率化する方法を解説
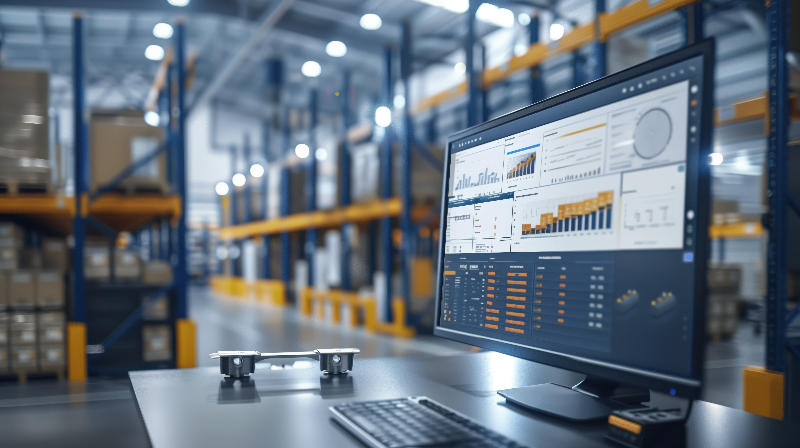
課題と解決策を解説
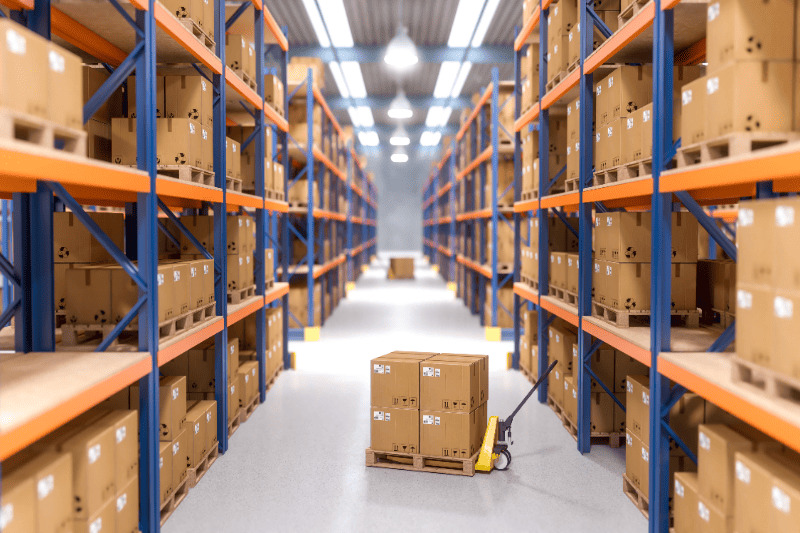
よくある課題、効率化する方法を解説