予防保全とは?
製造現場に潜むリスクをRFID活用で低減
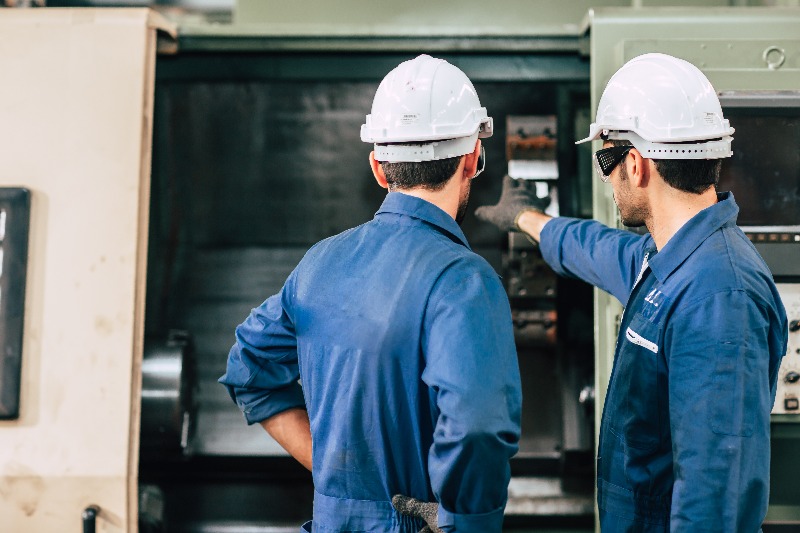
工場の安定かつ継続的な稼働を目的として行う保全方法である予防保全。本記事では、予防保全の概要や目的、種類、メリットについて解説します。また、予防保全業務を効率化するRFIDの活用方法についても解説します。

予防保全とは
予防保全とは、工場の設備や機械、部品ごとに耐用年数や耐用時間を定めたうえで、一定の期間使用をしたら故障していなくても交換する保全方法のことです。また、決められた期間や内容にて保守・メンテナンスを定期的に行うことも予防保全と呼ばれています。
以下では、予防保全の目的や種類、メリットなどについて解説します。
予防保全の目的
予防保全の目的は、工場や生産現場の設備や機械を安定して継続的に稼働させることです。工場の設備や機械、部品などが故障・停止するとモノづくりの品質低下につながるだけでなく、納期の遅延につながりかねません。このようなトラブルを回避するためにも、定期的かつ徹底した予防保全を行う必要があります。
予防保全の種類
予防保全には、「時間基準保全(TBM)」、「利用基準保全(UBM)」、「状態基準保全(CBM)」の3種類があります。
●時間基準保全(TBM)
時間基準保全(TBM)は、時間を基準にしてメンテナンスを行います。
基準となる時間の間隔が長すぎると、予期せぬ故障が発生する可能性があり、逆に短すぎると故障は回避できますが、無駄なメンテナンスコストがかかります。そのため、時間基準保全を行う際は、適切な時間基準を設定することが重要です。
たとえば、治具・取付工具の耐用年数は「3年」と定められているため、この期間が適切な時間基準として設定することが必要です。
●利用基準保全(UBM)
利用基準保全(UBM)では、機械や設備、材料の利用回数や利用量に応じてメンテナンスを行います。
適切な利用基準保全を行うためには、対象となる機械がどのくらい使用されたのか徹底的に記録・管理することが重要です。
たとえば、プレス加工を行う金型などはショット数を記録・管理することでメンテナンスの時期を把握することができます。
金型のメンテナンスや管理については以下でご紹介しています。あわせてご覧ください。
●状態基準保全(CBM)
状態基準保全(CBM)は、機械や設備、部品の状態を管理することで、状態が悪化したものを修理、交換をする方法です。
利用環境や製造品目の違いによって、同じ稼働時間や同じ利用回数でも劣化の度合いが異なるため、リアルタイムでの状態把握が重要です。状態基準保全を効率よく行うためには、後述するRFIDの活用が重要です。
予防保全以外の2つの保全
以下では、ご紹介した予防保全以外の保全方法を2つご紹介します。
●予知保全
予知保全とは、工場や生産現場の設備、機械の故障の兆候を事前に検知したうえで保全することです。故障しないように事前に保全するという点では予防保全と同じです。
予知保全と予防保全の違いは「きっかけ」の違いです。
予知保全は動作や音といった故障の兆候をきっかけに行う一方で、予防保全は時間や利用回数など基準が保全のきっかけとなります。
●事後保全
事後保全とは、工場や生産現場の設備、機械の「故障」「生産能力の低下」「不良品発生」などのトラブルが発生したときに行う保全業務です。
予防保全では、故障しないように事前に保全を行いますが、事後保全は故障したときの保全業務であるため、目的やタイミングが異なります。
また、事後保全は起きてはいけない事象が発生してしまうことを認識し、注意する必要があります。
予防保全と予知保全、事後保全と3タイプの保全方法をご紹介しました。
故障の予兆や発生をきっかけとする予知保全、事後保全は問題が起きた際に復旧作業に時間や工数が発生する可能性があります。
しかし、故障の発生に関わらず一定期間でメンテナンスを行う予防保全では、復旧作業による作業工程が止まってしまうというリスクが無いということが最大の違いとなります。
以下ではこの予防保全のメリットをご紹介します。
予防保全のメリット
予防保全を行うことのメリットは数多くあります。
たとえば、予防保全を通して定期的なメンテナンスを行い、突然の故障や不具合を防止できれば、製品の品質担保につながります。また、事前に故障を防ぐことで、生産停止によるダウンタイムが発生せず、生産性の向上につながることも予防保全のメリットです。
さらに、予防保全は定期的に行うため、スケジューリングを明確に行うことができます。そのため、突発的なトラブルが発生し、夜間や休日に急な対応を迫られる心配もありません。
上記でご紹介したようにさまざまなメリットがある予防保全ですが、適切なタイミングかつ、徹底するためには、管理工数や人的工数がかかります。そこで重要なのが「RFID活用」です。
予防保全を効率よく運用する「RFID活用」
予防保全はRFIDの活用によって効率よく行うことができます。
たとえば、工場の機械や設備・部品にRFタグを使用し、機械や設備・部品の利用時間、利用回数、状態など予防保全を行うために必要な情報をリアルタイムかつ簡単にデータ収集できます。RFIDを通してデータとして可視化されるため、管理コストや人的コストの低減だけでなく、適切なタイミングで徹底的な予防保全が可能です。
以下ではRFIDを含むIoTやIT技術を活用した、製造現場の業務を効率化する「みえる化」についてご紹介しています。ぜひ、あわせてご覧ください。
次章ではRFID活用によって具体的にどのような予防保全ができるのか事例をご紹介します。
RFID活用による予防保全事例3選
事例①:先入れ・先出しの予防保全
1つ目は、RFIDを活用した先入れ・先出しのみえる化による予防保全です。
いつ製造したのかといった情報をRFタグに書込み、部品に取り付けることで、部品の使用期日や製品の状態管理が容易になり、予防保全を正確かつ効率的に行えます。
また、RFIDによる先入れ・先出しのみえる化は、予防保全の効率化の他に、廃棄リスクの低減も可能です。以下記事ではその詳細についてご紹介しています。
事例②:通い箱の予防保全
通い箱やパレットの紛失トラブルに対する予防保全にもRFID活用は有効です。
工場で利用されている通い箱やパレットは、利用状況が不明なことによりムダな経費が発生しているケースが多いです。通い箱やパレットにRFIDを活用することで資材がいつ、どこに出荷され、どのくらいあるのかなど利用情報がみえる化され、情報を正確に把握・管理ができます。また、正確な情報管理によって、必要な通い箱・パレット数の把握も可能です。
通い箱・パレットにまつわる課題やトラブルについては以下でご紹介しています。
通い箱・パレットといった循環輸送資材のみえる化は、以下ソリューションの導入によって実現できます。
事例③:金型の予防保全
金型の予防保全にもRFIDは活用可能です。
金型には限界ショット数という寿命の目安が決まっており、ショット数によってメンテナンスを行わなければなりません。しかし、多くの現場ではショット数を手入力で管理し、管理者の属人性によってメンテナンスや廃棄が行われているケースが見られます。
RFIDを活用することで、ショット数の実績管理を徹底できるため、適切な予防保全が可能です。
このような金型に関するRFID活用は、以下資料や記事で詳しくご紹介しています。ぜひ、あわせてご覧ください。
予防保全のRFID活用は
小林クリエイトまでご相談ください!
ご紹介したような予防保全におけるRFID活用は全て、小林クリエイトのソリューションによって実現可能です。また、予防保全などの製造業の悩みを解決するソリューションのご提案も行っているため、工場においての課題やお悩みがあればぜひ1度ご相談ください。
以下にてダウンロードできる資料は、製造業におけるRFID活用の詳細についてまとめています。
ご関心のある方はぜひご覧ください。
お役立ち資料はこちら
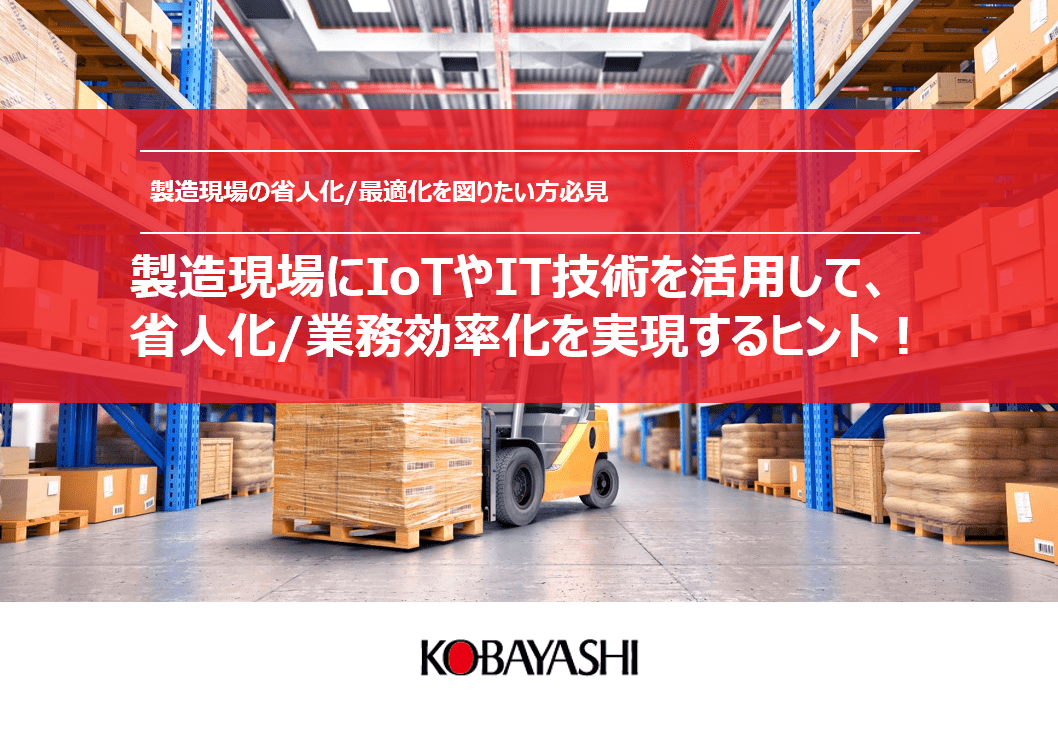
お役立ち資料
省人化/業務効率化を実現するヒント!

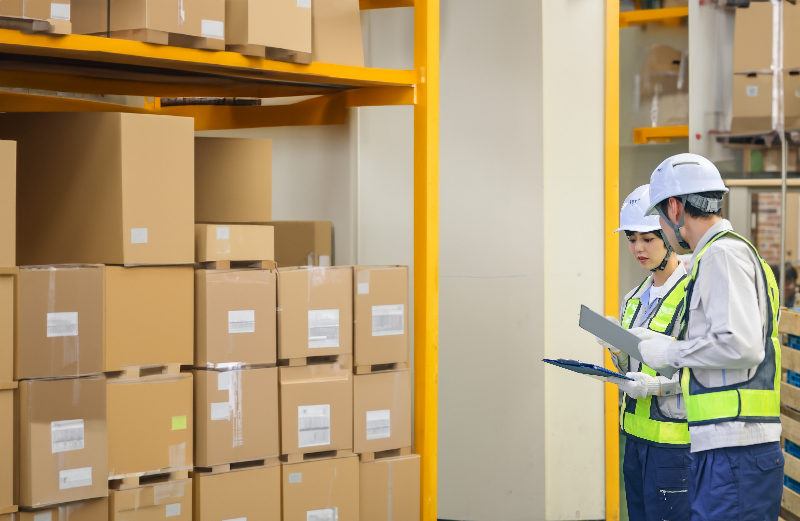
対策とは?
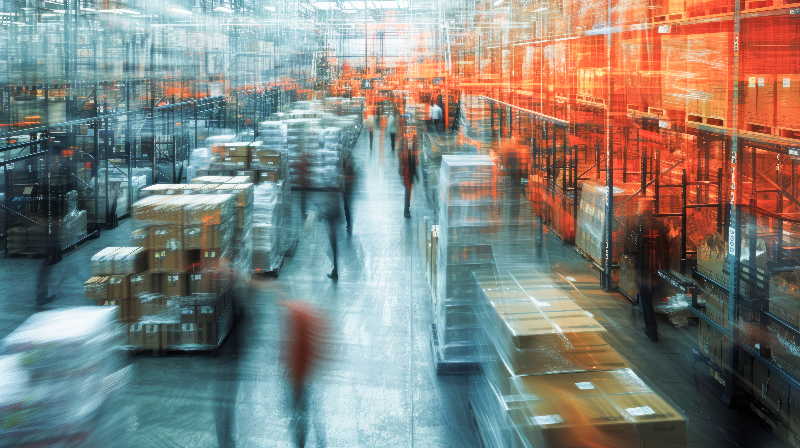
発生する原因と影響、対策を解説
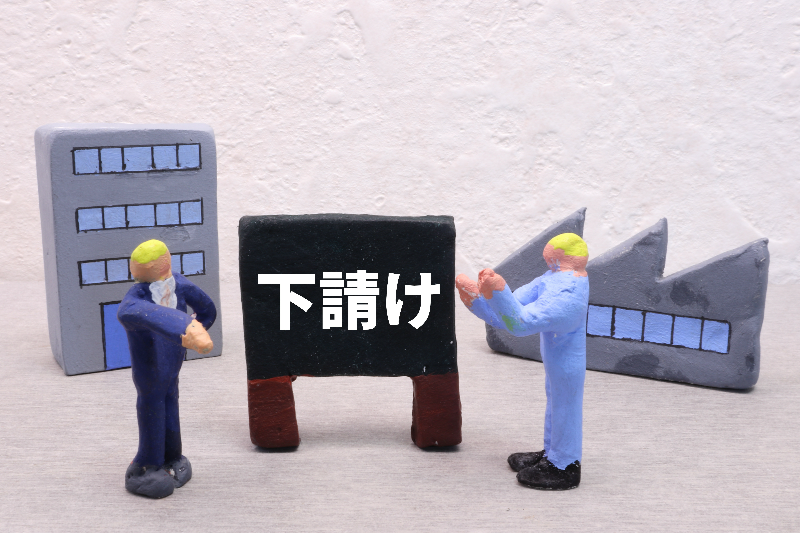
適切に行うポイントとは?