倉庫業務を効率的に行うための
物流改善方法のご紹介
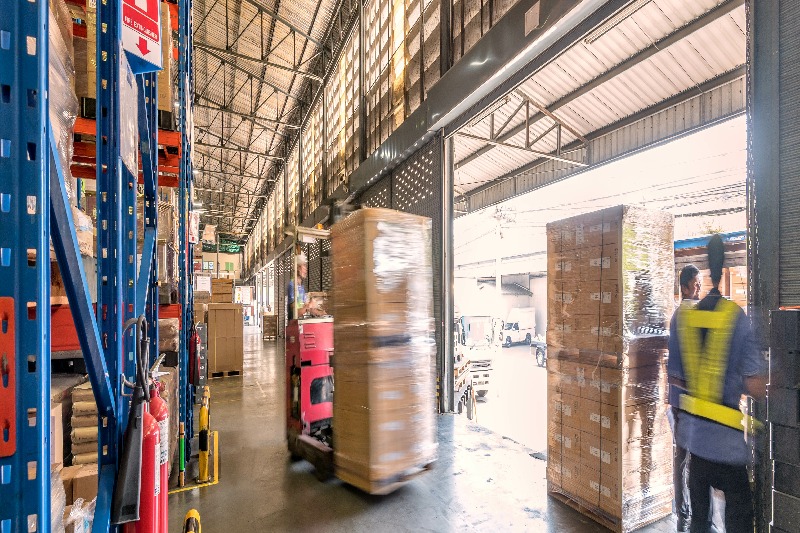
製造・物流業における倉庫業務は、3Mやヒューマンエラー、業務の属人化などさまざまな課題が発生しており、効率化がなかなか進まないケースがあります。本記事では、倉庫業務を効率化したいと考えている企業の担当者様に向けて、課題の改善方法や、課題解決につながるシステム・ツールをご紹介します。

倉庫業務においてよくある5つの課題
製造・物流業の業務の1つに倉庫内の業務があります。
この倉庫業務は、庫内搬送や、在庫管理、入出荷管理などさまざまな作業に分かれていることから、どの倉庫でも多くの課題が発生しているのが現状です。
そこで以下では、倉庫内業務にて発生することの多い課題を5つご紹介します。
3Mの発生(ムリ・ムダ・ムラ)
1つ目の課題は3Mの発生です。
理想的な物流倉庫の作業環境は、「負荷(作業量)」と「能力(キャパシティ)」が均衡していて、常に問題なく業務が遂行されている状態です。しかし、多くの倉庫では、能力以上に負荷がかかっている「ムリ」、能力に対して負荷が下回っている「ムダ」、作業が不安定な状態で稼働している「ムラ」という3Mが発生しています。
物流現場における3Mについては以下の記事でもご紹介しています。こちらもあわせてご覧ください。
ヒューマンエラーの発生
倉庫業務でよくある問題として、ピッキングミス、チェックミスがあげられます。これらのミスはヒューマンエラーが原因です。
倉庫業務の確認作業は人の手によるものが多く、ヒューマンエラーが起こりやすい状況にあります。また、在庫の置き場所がわかりにくい、作業が煩雑、ルールが徹底されていないといったこともヒューマンエラーにつながりやすいといえます。
以下記事では、ヒューマンエラーの中でも誤品について解説しています。こちらもあわせてご覧ください。
モノの所在把握ができていない
倉庫業務は属人化しやすく、倉庫内のモノ(在庫や道具)が個人によって管理されている状態になっていることがよくあります。そのため、倉庫全体でモノの所在管理ができておらず、属人化しているスタッフが不在になるとトラブルや生産性の低下などが起こりやすくなります。
人手に頼っている業務が多い
昨今では、IoTやAIなどの技術の発展によって、システムによる業務の自動化が進んでいます。
しかし、物流現場は、そのような将来的な投資が行いづらいのが現状であり、納期遵守や品質管理といった目の前の課題が優先されています。したがって、未だに人手に頼っている業務が多く、生産効率の向上が進んでいないケースが多いです。
適正な在庫数の把握が困難
先述したように、倉庫では属人化した在庫管理が行われている場合が多いです。
また、管理されていたとしても、Excelでの手動入力による管理であるため、実数とデータ上の数が一致するまでタイムラグがあり、齟齬も起きやすいという問題があります。
そのため、生産実績に応じた在庫の適正化が難しく、多くのコストのムダが発生したり、業務に支障が生じたりしています。
▼関連記事はこちら
製造業の在庫管理を解説 -管理方法やシステムによる業務改善アイデアを紹介-
倉庫の棚卸業務を効率化する方法とは?改善のポイントと解決に向けたアイデアをご紹介
入荷作業を効率化するためには?ポイントと事例をご紹介
出荷業務のムダを省くヒント
倉庫業務の効率化を実現する改善方法7選
以降では、先ほどご紹介した課題の解決に向けて、物流現場が行うべき解決策を7つご紹介します。
特に、ご紹介する①~③は、倉庫内業務を効率化するために必要不可欠なものです。
①:5Sの徹底
倉庫業務の効率化に向けて、まず行うべきことは、5Sの徹底です。5Sとは、「整理・整頓・清掃・清潔・しつけ」の5つの行動のことです。それぞれの頭文字がいずれもSとなっていることから5Sと呼ばれています。
この5Sを徹底することで、現場内での作業がしやすい空間になり、業務効率化を行うための体制を作り上げることができます。また、5Sの見直しは業務効率化だけではなく、事故の防止や、従業員の意識上昇などの効果も期待できるため、労働災害が多い傾向にある倉庫現場では重要な要素です。
②:ロケーションの見直し
5Sが徹底されたら、倉庫内の在庫の保管場所などのロケーションの見直しを行うべきです。保管場所が適切でなければ、無駄な移動や、管理が発生しており、生産性の低下を起こしてしまいます。
全ての人が作業しやすく、最小限の負担にできるような作業導線の適正化を検討すべきでしょう。
③:作業マニュアルの作成
5Sが徹底され、ロケーションが最適化されても、その業務自体を従業員がそれぞれのやり方で行っていては、作業にムリ・ムダ・ムラの3Mが発生してしまいます。
そのため、誰でも同じ生産効率で作業ができるように、業務の標準化を行うことが重要です。具体的な方法としては、マニュアルの作成が挙げられます。作業の標準化を行うことで、属人化の防止や新人教育の効率化につなげられます。
ここまでご紹介した①~③は、作業効率化に向けた第一歩と言えます。現状の倉庫業務の改善を検討している場合は、まずこの3点の見直しを行いましょう。
以降でご紹介するのは、現在の業務をテクノロジーの活用によって効率化する方法です。イニシャルコストがかかりますが、倉庫業務の大幅な効率化や生産性向上の効果が期待できます。
④:バーコード照合の活用
1つ目は、バーコード照合による現場での納入品確認をはじめとした、各種チェック作業を効率化する方法です。
従来のチェック作業は、現品票と集荷リストを目視で確認しながら行っていたため、時間がかかり、ヒューマンエラーが発生しやすいものでした。
そのような状況に対して、二次元コードやバーコードを導入することで、確認作業を効率化し、ヒューマンエラーも減らすことができます。具体的には、集荷時に現品票に記載されている情報を集荷リストとして登録することでバーコード照合が可能となり、確実な集荷・出庫履歴の取得を実現します。
このようなバーコード照合については以下の資料をご覧ください。
⑤:RFIDの活用
次はRFIDによる在庫管理・所在管理を効率化する方法です。
在庫管理・所在管理にて自動認識技術であるRFIDを導入することで、在庫の状態がみえる化されるため、管理工数の削減、作業の効率化、リアルタイムな所在管理が実現します。
在庫管理・所在管理におけるRFIDの活用は以下記事でご紹介しています。こちらもあわせてご覧ください。
⑥:音声認識技術の活用
倉庫業務でよくあるピッキングや仕分け作業・荷受け作業は音声認識技術の導入による効率化ができます。
従来、これらの作業は表をチェックしながら在庫を確認し、それを手作業で入力する必要がありました。そのため持ち替えなどが多く発生し、データ入力も改めて別のシートに転記する必要もあるなど、多くのムダが発生していました。
そこで、音声認識を導入することで、これらの作業の入力作業はハンズフリーにて可能となり作業効率が向上します。また、音声入力したものは、自動で管理シートに反映されるため、発生していた無駄な工数をそのまま低減できます。
以下記事では音声認識技術による現場作業効率化の事例をご紹介しています。ご興味のある方はぜひご覧ください。
⑦:システムによる実績管理
システムによる倉庫内工程の実績収集を行うことで、現場の作業を効率化することが可能です。
具体的には、作業開始・終了時に製品のバーコードなどを読み取り、作業開始・終了時刻をシステムが記録します。このように作業ごとの実績をシステムが記録することで、作業の的確な進捗管理を行うことができ、改善や効率化につなげることができます。
物流現場の改善も小林クリエイトにおまかせください!
本記事では、製造・物流業における、倉庫作業の課題や効率化を行うための方法をご紹介しました。今回ご紹介した方法について、小林クリエイトでは、そのサポートやシステムの導入支援などを行っています。
小林クリエイトは、自動車関連業界をはじめとした製造業界全般で、業務効率化・コスト低減など現場改善のプロフェッショナルとしてサポートしており、そのノウハウを倉庫現場に活かし、業務効率化に向けた提案ができます。業務効率化を実現したい企業の担当者はぜひ一度ご相談ください。
以下資料では、今回ご紹介したようなRFIDを活用した現場改善事例を解説しています。ご興味のある方はぜひご覧ください。
お役立ち資料はこちら
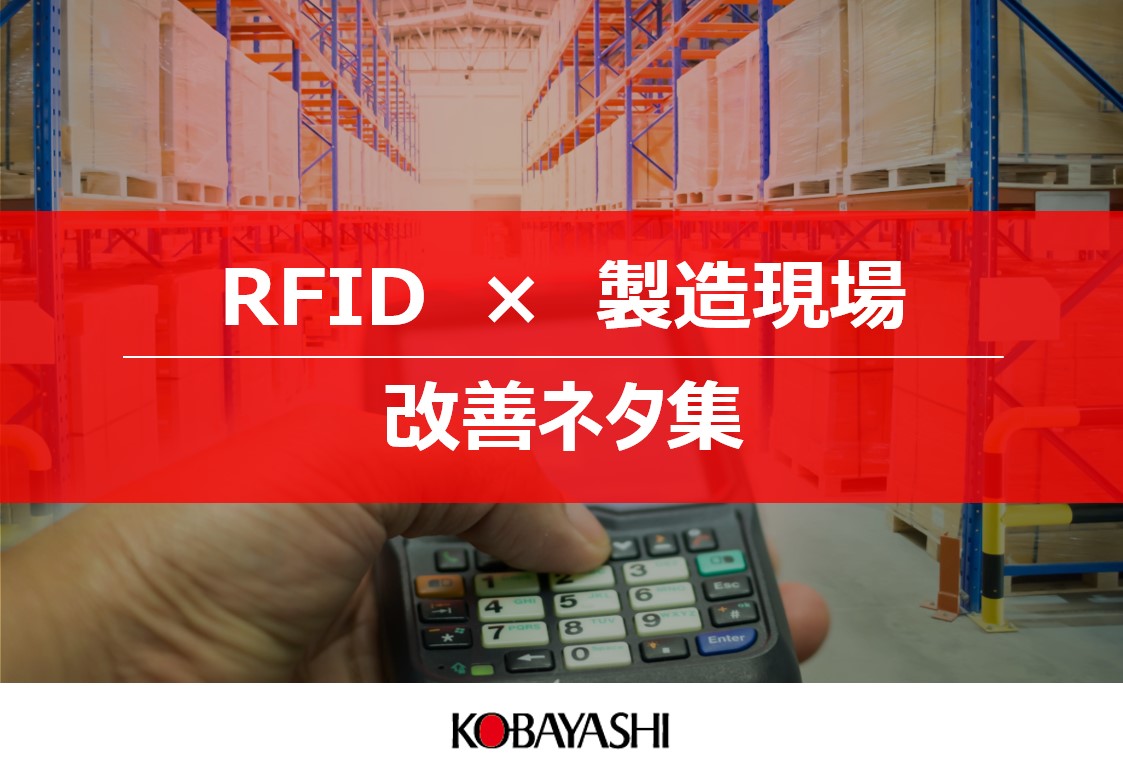
お役立ち資料
改善ネタ集

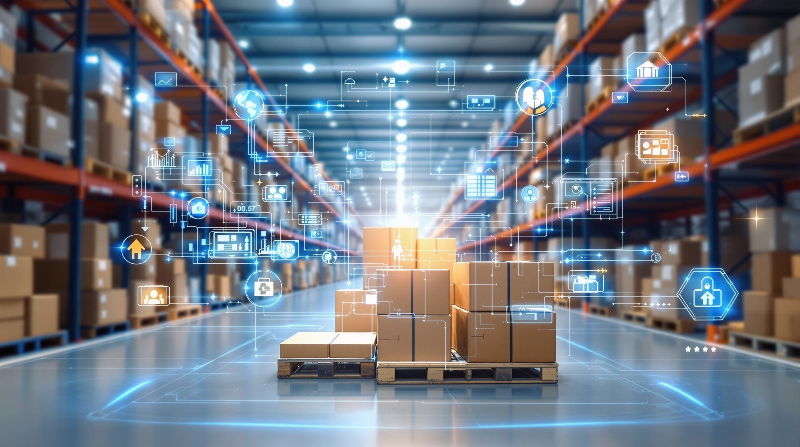
業務内容や効率化する方法を解説
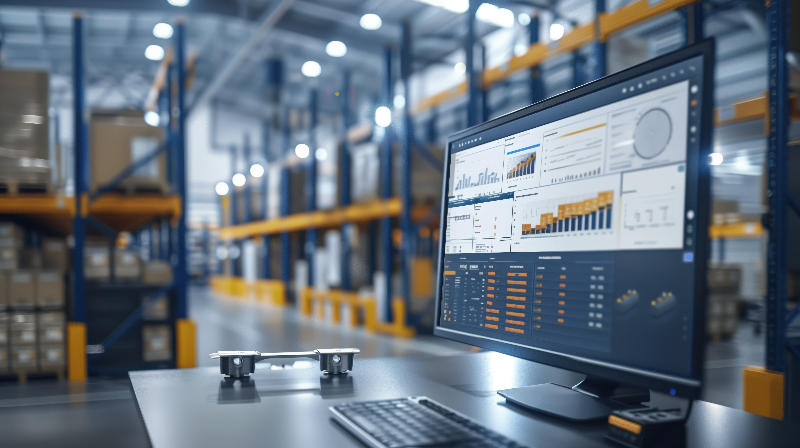
課題と解決策を解説
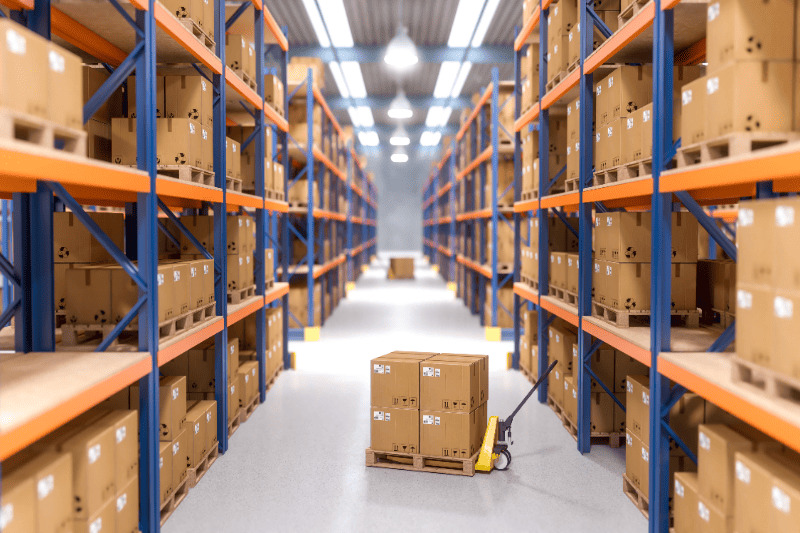
よくある課題、効率化する方法を解説