ポカヨケとは?
製造業のヒューマンエラー対策の事例をご紹介
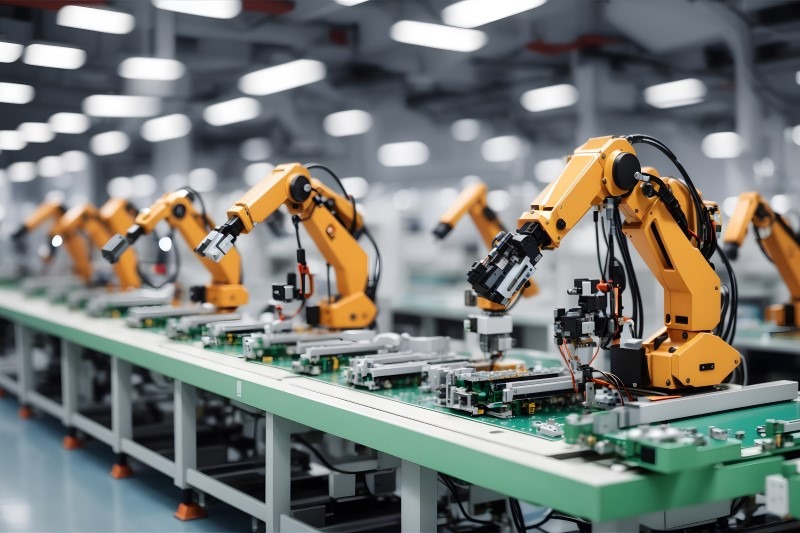
製造現場でのヒューマンエラーを削減し、重大な事故を未然に防ぐためには「ポカヨケ」が非常に重要です。ポカヨケを徹底することで不良品の発生やラインの停止などを避けられるため、品質の安定や生産性の向上にも貢献します。本記事では、そうした重要性をもつポカヨケを徹底する対策や事例をご紹介します。

ポカヨケとは
はじめに、製造現場でしばしば見聞きする「ポカヨケ」とはどのようなものなのか見ていきます。
ポカヨケとは「ヒューマンエラーを未然に防止する仕組み」
ポカヨケとは、確認不足や不注意によって生じるヒューマンエラー=ポカミスを未然に避ける仕組みのことです。ポカヨケはトヨタ生産方式の一つであり、製造業の現場で古くから実践されてきました。
よくある「ポカ」としては、発注ミスや異物の混入、検品での不良品の見落とし、作業手順の間違いなどがあります。
1つひとつのポカは製造現場や経営に大きな影響を与えるものではないものの、ポカを放置して対策を取らないと軽微な事故が発生し、いずれ重大な事故につながる可能性があります。
ビジネスにおけるリスクマネジメントで有名な「ハインリヒの法則」では、1つの重大事故が発生する前には29の軽微な事故があり、さらにその背後には300の異常が存在するといわれています。この異常にはポカやヒヤリ・ハットが該当するため、意図しない大事故を防ぐためにもポカヨケは非常に重要といえます。
ポカをはじめとする製造業のヒューマンエラーへの対策については、以下の記事で詳しく解説しています。
ポカヨケの基本的な考え方
ポカヨケには、人為的なミスの発生前と発生時、発生後の各段階に応じて、対応方法の基本的な考え方があります。
- 発生前対策:ミスを発生させない
事前に起こり得るリスクを想定したうえで、物理的にポカが発生しない部品の形状にする、作業者がミスをしたら次の工程に進めなくするなどの仕組みを作ることが重要であると考えます。 - 発生時対策:ミスが発生したらすぐ発見されるようにする/適切な対応をする
ミスをすぐに発見できるように、ポカを検知するための画像認識や光学センサーを導入したり、警報音や信号灯を導入したりするなど、視覚・聴覚に訴えて周知する仕組みを取り入れることが効果的とされます。 - 発生後対策:ミスの影響範囲を最小限にする
ポカが発生してしまったとしても、その影響を最小にとどめることが重要と考えます。具体的には、製造ラインの後の工程(製品の包装や出荷工程)で不良品を検知し、排除する仕組みなどが必要とされます。
ポカヨケに取り組む目的
ポカヨケに取り組む目的としては、主に以下の3つがあります。
- 品質保証の強化
ポカヨケは製品の品質を安定させるうえで不可欠です。ポカヨケを実施することによって、生産ラインでの手順やルールの逸脱を防ぐことができます。その結果、不良品の発生を最小化でき、発生した場合にも適切に取り除くことで不良品が流通するのを防ぐことが可能です。これにより製品の品質が安定し、品質保証の強化につながります。 - 生産性の向上
ポカミスが発生すると、生産ラインを停止するなど、作業を中断してリカバリーしなくてはなりません。生産性が低下します。ポカヨケによって作業のミスをなくすことでダウンタイムが減り、生産性向上に寄与します。 - 安全性の確保
不適切な操作や作業手順の間違いなどは重大な事故の原因になりかねません。ポカヨケによって操作や作業手順の誤りをなくす仕組みを構築することで、事故の発生を防ぎ、従業員の安全を確保できます。
また、ミスを防ぐ仕組みがあることで従業員の負担を軽減し、疲労から生じる事故を防ぐことにもつながります。
ポカヨケを徹底する!ヒューマンエラー対策
ポカヨケを徹底するためにはどうすれば良いのでしょうか。以降では、具体的な4つの対策をご紹介します。
専用治具の取り付け
組立・加工の際に使う治具は、逆向きに取り付けてしまうなどポカミスの原因になることがあります。そこで、組み付けの間違いなどを防止することが重要です。
例えば、部品にガイドピンや突起を付けて、正しい方向にしか部品を組み付けできないようにして不良品の発生を防ぐ対策や、特定の部品のみに使える形状に変える対策などが挙げられます。
置き場所の固定や色分け
組立や加工に使用する部品を間違った場所に置かないように置き場を固定したり、良品と不良品を区別しやすいようにケースを色付けしたりすることもポカヨケとして効果的です。これにより、本来使うべきでない部品を組み立てに使うことや、後工程に不良品が混入することを防げます。
バーコード・二次元コード・RFタグの導入
バーコードや二次元コード、またはRFタグを製品・部品に取り付けることで、より正確な識別や更新作業が可能となります。例えば、RFタグを読み取ることで金型管理をシステム化できれば、金型のメンテナンス時期を把握できます。これによりサビや汚れの発生・付着を防げるため、不良品の発生を抑えられます。
また生産管理システムと連携し、作業漏れがあった場合にも後工程に通知される仕組みにすることで、重大なミスの発生を防ぐこともできます。
RFタグを製品・部品に取り付ける際には、使用環境や対象物の材質ごとに適切なものを選定する必要があります。RFタグ・ラベルの選定方法は以下の資料で解説しています。
IT・IoTシステムの導入
IT・IoTシステムを導入し、工具のIoT化を進めることも有効です。例えば、工具と外部端末を通信可能にすることで、作業者が自身の作業内容をデータとして確認でき、締め付け回数をカウントしたり、誤組み付けを阻止したりできます。このように、IT・IoTシステムにより作業内容を可視化することで、ミスの発生を防止できます。
ポカヨケの事例
以下では、小林クリエイトでのポカヨケ事例を3つご紹介します。
①先入れ先出しの徹底による不良流出防止
先入れ先出しは、先に保管されたものから順に使用もしくは出庫し、長期保管に伴い保管物の品質が劣化することを防ぐ管理手法のことです。先入れ先出しが徹底されていないと、品質の劣化した原材料が製品に使用されてしまい、製品そのものの品質に大きく影響を及ぼす可能性があるため、先入れ先出しは重要なポカヨケの1つです。
具体的には、入荷時に使用期限の情報を埋め込んだRFタグを対象物に取り付け、使用する際に専用の機械で読み取ることで、先入れ先出しの徹底が容易になります。
先出し先入れの詳細については以下の記事をご覧ください。
②RFIDを活用したフォークリフトの事故防止
RFIDを活用して、フォークリフトの運転手と周囲の人間の双方に対象物が接近していることを知らせ、接触事故を回避する仕組みを構築することも可能です。
具体的なソリューションとしては、「RFID検知信号灯鳴動システム」があります。これを事故が発生しやすい場所に設置することで、信号灯の鳴動によりフォークリフトなど対象物が接近していることを知らせることができます。
RFIDを活用したフォークリフトの事故を防ぐ仕組みについては、以下の記事で詳しく解説しています。
③バーコードや二次元コードを活用した誤品防止
バーコードや二次元コードを活用した誤品防止も効果的なポカヨケ対策です。
「誤品照合システム ハブリッジ」は、ハンディーターミナルを活用してバーコード・二次元コードの読取ができるシステムであり、確実な集荷&出庫履歴の取得ができるようになります。製品出荷時の現品票差し替えチェック、製品入出庫置き場のチェックなど、都度出荷データと照合し作業が進められるようになり、納入先が増えても誤品のリスクを低減できます。
バーコードや二次元コードを活用した誤品防止対策については、以下の記事で詳しく解説しています。
こちらの資料では、ポカヨケをはじめ、製造業の品質管理や生産効率向上を図るうえでの現場改善アイデアをご紹介しています。ご興味のある方はぜひご覧ください。
お役立ち資料はこちら
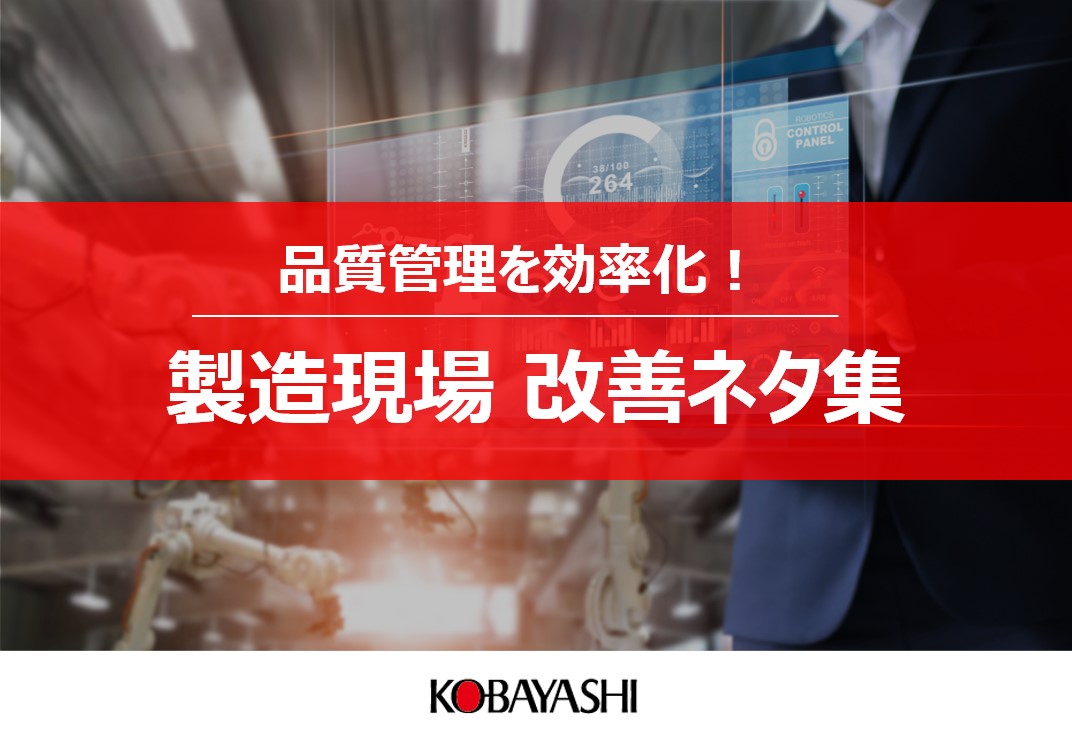
お役立ち資料
製造現場 改善ネタ集

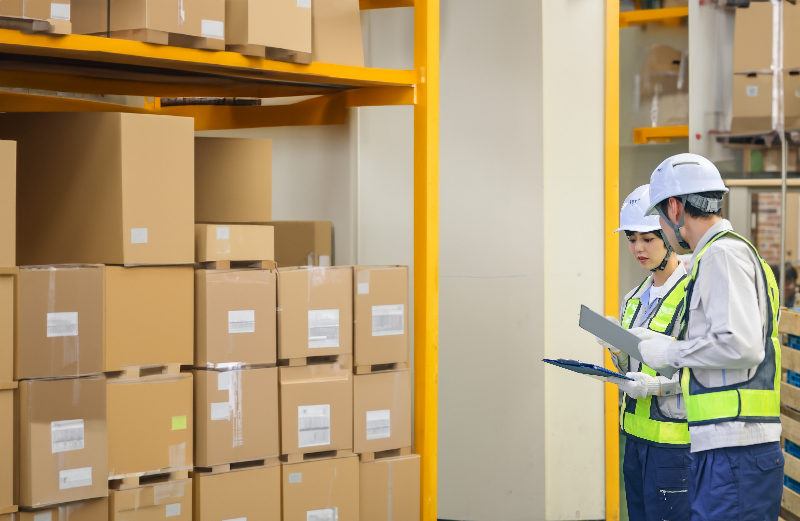
対策とは?
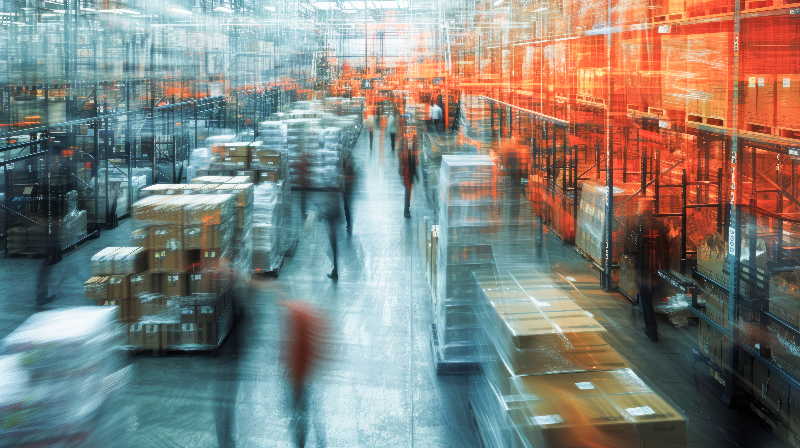
発生する原因と影響、対策を解説
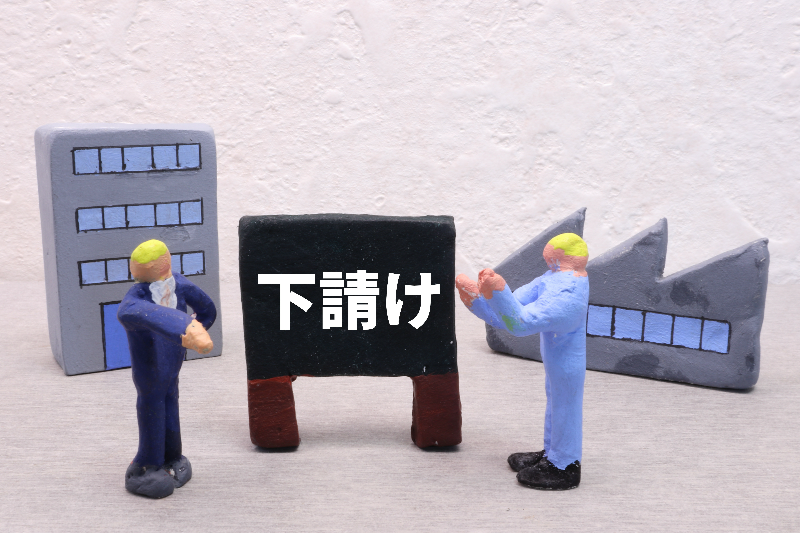
適切に行うポイントとは?